In today’s fast business environment, an orderly, efficient, and productive workspace is very important for everyone. One of the most known methodologies for this is the 5S methodology. This comes from Japan. The 5S system basically explains what to do, how to do it, how to implement it in order to increase productivity by making sure that the workplace is clean, organized, and efficient. However, the 5S could be implemented in any industry.
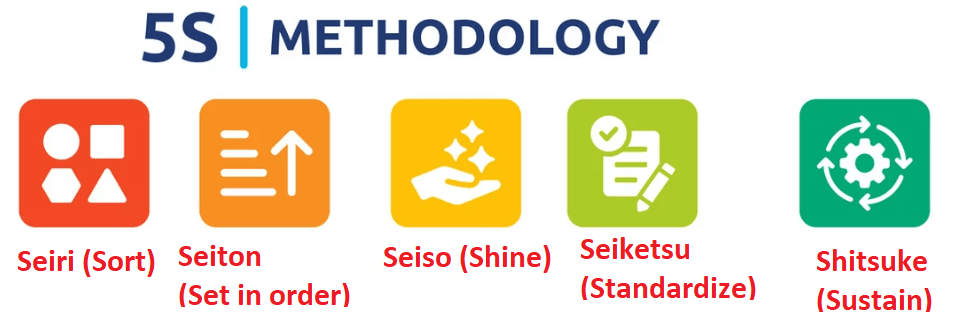
What is 5S?
The 5S methodology contains five principles, each starting with the letter “S”. These principles guide organizations to create a systematic and effective environment in organization. The five steps of 5S are as below:
- Seiri (Sort)
- Seiton (Set in order)
- Seiso (Shine)
- Seiketsu (Standardize)
- Shitsuke (Sustain)
Each of above principle addresses a specific aspect of the workplace, aiming to create an environment that minimizes waste, increases efficiency, and promotes safety.
1. Seiri (Sort): Eliminating Unnecessary Items
The first step of the 5S methodology is Seiri or Sort, which focuses on the identification and removal of not required items in the workspace. This is the step where the workspace separates what is required from what is not. An unorganized workspace leads to confusion, lost time, and even safety hazards. Sorting involves the following:
- Evaluating equipment, tools, and materials in the workspace to decide what is critical for the routine tasks and can be removed or discarded.
- Separate items into two sections: “required” and “not required.” Not required: items that were not used even after a very long time. They may be not needed hereafter.
- Throw away, recycle, or rearrange the things that are in the “not required” column to make an organized and debris-free workspace.
Removing unnecessary means employees will have the ability to focus what’s important and will therefore produce more with fewer errors.
2. Seiton (Set in Order): Organizing the Essential
Once the unnecessary items are removed, the next step is Seiton, which means “Set in Order”. This principle focuses on arranging and organizing the essential items in the workplace for easy access and maximum efficiency. It includes:
- Arranging tools and materials in a logical, standardized way that reduces the time spent searching for items.
- Designate particular spaces for different items, giving each item an assigned place so that everything’s in its spot. Labels or color-coding or numbering them can help one locate what’s needed quickly for the workers.
Implement visual control by using shadow, outline and labeling to explain where tools would be placed ensuring nothing gets lost. - Organizing the work environment helps people avoid wasted time and frustration by creating more productive workflows.
3. Seiso (Shine): Cleaning and Maintaining the Workplace
Seiso, or Shine, addresses the cleanliness and maintenance of the workplace. A clean workspace is not only an important safety requirement but also adds to the productivity and morale of employees. It can also recognize potential problems that may be unseen, such as equipment failure or hazards. Some of the responsibilities include:
- The cleaning of desks, equipment, and tools.
- Cleaning equipment for inspection for any maintenance requirement or wear and tear.
- Constantly keeping the workplace clean so that it remains tidy and hygienic at all times.
A clean workplace will help to have a healthy environment, reduce accidents, and ensure that employees work in a place that allows them to focus without distractions or hazards.
4. Seiketsu (Standardize): Establishing Procedures for Consistency
Once the first three steps are followed, it becomes essential to standardize the practices in order to sustain the improvements done. Seiketsu or Standardize, involves the process of developing standardized procedures and practices so that the processes of sorting, setting in order, and shining continue to be carried out. This includes:
- Development of standard operating procedures (SOPs) describing how the 5S principles should be followed by everyone within the organization.
- This training will make sure that employees know the importance of 5S and proper procedure to be implemented so that each employee is implementing the same process.
- Periodical audits are required to ensure standards are followed. Any deviation requires quick correction to the process.
Thus, standardizing the practices within an organization allows the benefits of 5S to be sustainable over time, rather than letting them fade because of lack of discipline or lack of consistent practice.
5. Shitsuke (Sustain): Creating a Culture of Continuous Improvement
It stands for Sustain, or Shitsuke in Japanese, which is the final step of 5S methodology. This step involves making 5S a habit and part of the organization’s culture to make sure the improvement from the other four steps are sustained over time. Without it, any improvements done by the other four steps will not last long. Sustaining 5S involves:
- Create a culture of discipline, where all employees take responsibility to maintain the 5S standards and continually improve their work environment.
- Review and improve the 5S system regularly, as changes are observed in the workplace.
- Encourage employee involvement to suggest improvements in the system; create a sense of ownership and responsibility for the workplace.
It helps organizations ensure long-term success, continued efficiency and ongoing workplace improvements by sustaining the 5S system.
Benefits of Implementing 5S
The implementation of the 5S methodology provides a number of benefits to any organization:
- Improved Productivity : Eliminating unnecessary items, proper organization of tools, and cleanliness in the work environment ensure employees do not waste time on the tasks, resulting in faster completion of work with greater efficiency.
- Safety Improvement : A clean and organized workspace eliminates accidents and risks. Proper maintenance of equipment and clear pathways minimize the potential for workplace injuries.
- Cost Reduction : 5S leads to the elimination of waste, eliminates downtime, and reduces unnecessary waste on tools and equipment not used. It gives the organization large cost savings.
- Improved Morale and Motivation : It makes the working environment comfortable, motivating, clean, and productive. Such conditions may boost employee job satisfaction and engagement, leading to improved morale and motivation.
- Improved Quality : Clearness through 5S allows employees to easily access the appropriate tools and materials, eventually reducing errors and eventually improving quality in the products or services provided.
Conclusion
The 5S methodology is something more than being a system that cleans and organizes; rather, it embodies a philosophy with the principles of discipline, constant improvement, and a culture of efficiency. Applying 5S to an organization will transform your workplace into one that is efficient, safe, and high-performing. With such a proven history of efficiency gains, waste elimination, and enhancement of employee morale, 5S is surely a valuable resource for any company seeking to succeed in today’s fast-paced and competitive world.
Whether a factory, office, or any working place, the 5S approach at work improves operational efficiency and a work culture over long periods of time.
What Is Six Sigma? Concept, Steps, Examples
Frequently Asked Questions (FAQs) about the 5S Methodology
1. What does 5S stand for?
5S stands for five Japanese words: Seiri (Sort), Seiton (Set in Order), Seiso (Shine), Seiketsu (Standardize), and Shitsuke (Sustain). These principles focus on workplace organization and efficiency.
2. What is the main goal of the 5S methodology?
The main goal of 5S is to create a clean, organized, and efficient workspace that improves productivity, reduces waste, enhances safety, and promotes employee morale.
3. Where can 5S be applied?
Although 5S originated in manufacturing, it can be applied in various industries such as healthcare, offices, retail, education, and even at home to optimize organization and processes.
4. How does 5S improve workplace safety?
By eliminating unnecessary items, organizing tools and materials, and keeping the workspace clean, 5S reduces hazards, minimizes clutter, and ensures a safer work environment.
5. What are the benefits of implementing 5S?
Key benefits include:
- Increased efficiency and productivity.
- Improved safety and cleanliness.
- Enhanced employee satisfaction and morale.
- Cost savings through waste reduction.
- Higher quality in processes and products.
6. How does 5S differ from general housekeeping?
While general housekeeping focuses solely on cleanliness, 5S includes systematic processes like sorting, organizing, standardizing, and sustaining practices, making it a comprehensive methodology for workplace improvement.
7. What is the role of management in 5S implementation?
Management plays a crucial role by providing support, resources, and training. They must lead by example, monitor progress, and ensure that 5S becomes a sustained part of the organization’s culture.
8. How long does it take to implement 5S?
The time required varies depending on the organization’s size, complexity, and commitment. Initial implementation may take weeks to months, but sustaining it is an ongoing effort.
9. What challenges are commonly faced in implementing 5S?
Common challenges include:
- Resistance to change from employees.
- Inadequate training or resources.
- Lack of management support.
- Difficulty in sustaining the improvements over time.
10. Can 5S methodology evolve over time?
Yes, 5S is designed to be a dynamic system. As processes, technologies, and workplace requirements change, 5S can be adapted to meet new challenges and continue driving improvements.