Welding P91 material, a high-strength, heat-resistant alloy often used in high-temperature applications such as power plants, requires careful consideration of the welding process and the choice of welding electrodes. Both E9015-B91 and E9018-B91 electrodes can be used for this purpose, but E9015-B91 is preferred. Let’s delve deeper into the reasons behind this preference and explore the technical aspects of welding P91 material with these electrodes.\
Why Ni+Mn% is restricted in these electrodes
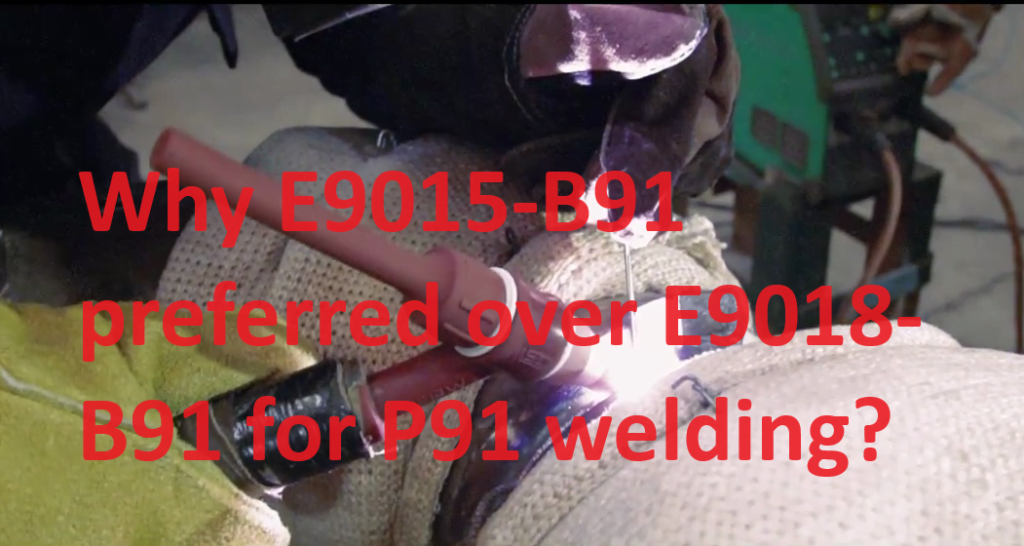
1. Coating and Iron Powder Content:
E9015 and E9018 electrodes have different coatings, which affect their performance and the resulting weld quality. The E9015-B91 coatings is “low hydrogen sodium” possess less iron powder and exhibit lower residual element content compared to E9018 electrodes which contains “low hydrogen potassium, iron power” coating. This lower iron powder content in E9015-B91 is advantageous because iron can lead to various undesirable effects, including grain boundary problems.
2. Residual Element Content:
The key difference between these two types of electrodes lies in their chemical composition, particularly in terms of residual element content. Residual elements in the weld metal can have a significant impact on the microstructure and mechanical properties of the weld. E9015-B91 keeping the residual element content low, specifically with a value of X- Factor less than 15, which helps to maintain properties like temper embrittlement.
3. Reducing Crater Cracking and Grain Boundary Phenomena:
One of the primary reasons for preferring E9015-B91 over E9018-B91 for welding P91 material is to minimize the occurrence of crater cracking and other undesirable grain boundary phenomena. Crater cracking is a type of cracking that occurs at the end of a weld bead during the solidification process. This type of cracking can lead to weld defects and reduced structural integrity, which is a significant concern when working with high-strength materials like P91.
4. Influence of Low Melting Constituents:
It’s essential to understand that P91 material is susceptible to a phenomenon called “Type IV cracking.” This cracking occurs in the heat-affected zone (HAZ) of the weld and is associated with the formation of certain precipitates at grain boundaries. These precipitates can reduce the ductility of the material and make it prone to cracking under stress.
Choosing the right welding electrode, such as E9015-B91, helps in controlling the formation of these detrimental precipitates and maintaining the integrity of the grain boundaries in the welded joint. The lower residual element content in E9015-B91 electrodes contributes to a cleaner weld with fewer impurities that can promote grain boundary issues.
In summary, while both E9015-B91 and E9018-B91 electrodes can be used for welding P91 material, the preference for E9015-B91 stems from its lower residual element content, reduced iron powder content, and the ability to minimize undesirable grain boundary phenomena. These factors collectively contribute to a more reliable and robust welding process when working with high-strength, heat-resistant materials like P91. Understanding the nuances of electrode selection and their impact on weld quality is crucial in ensuring the long-term performance and integrity of welded components in demanding applications.