Welding is a critical process used in various industries to join metals and create strong, durable structures. To ensure the quality and integrity of welded joints, various factors must be considered, and one of the most crucial steps in this process is preheating. Preheating in welding is a method of raising the temperature of the base metal before the actual welding takes place. This seemingly simple step can have a significant impact on the quality and longevity of welds. In this article, we will explore the importance of preheating in welding, its benefits, and the factors to consider.
The Basics of Preheating
Preheating is the process of heating the base metal to a specific temperature range before welding. This is typically done using a preheating device such as a torch or electrical resistance heaters. The temperature to which the metal is heated depends on the material being welded and the welding process being used. In most cases, the goal is to heat the metal to a temperature below its critical transformation point but high enough to reduce the risk of cracking during and after welding.
When Preheat is required?
Preheating is especially important when welding:
- Highly restrained weld joints.
- Base materials having high carbon equivalent
- High hydrogen content of weld metal.
- Thick materials (preheat varies by material type).
- Base materials that tend to be more brittle, such as cast iron.
Benefits of Preheating
Stress Reduction: Preheating helps reduce the thermal stress that occurs during welding. When a weld is made, the molten metal cools rapidly, causing it to contract. If the base metal is not preheated, this rapid contraction can result in the formation of cracks in and around the weld. Preheating helps slow down the cooling process, allowing for more controlled contraction and reducing the risk of cracking.
Hydrogen Elimination: Preheating can help remove moisture and hydrogen from the base metal. Hydrogen can be a significant contributor to weld cracking and other defects. By preheating the metal, you drive out moisture and hydrogen, improving the overall quality of the weld.
Improved Ductility: Preheating can increase the ductility of certain metals, making them less prone to cracking. Ductility is the ability of a material to deform plastically before fracturing. By increasing ductility, preheating enhances a material’s ability to absorb stress and strain.
Reduced Hardness: Preheating can also reduce the hardness of the heat-affected zone (HAZ) around the weld. A softer HAZ is less susceptible to cracking and is generally more desirable in many welding applications.
2) The slower cooling rate provides sufficient time to diffuse out the hydrogen from the weld metal without causing cracking.
3) It helps to reduce the shrinkage stresses that can lead to cracking and distortion especially in case of highly restrained joints.
4) Preheating introduces the necessary heat into the weld area to ensure proper penetration. This benefits thick materials and those that conduct heat quickly. By preheating, you can use less heat in the welding arc and still achieve optimal penetration, because the base material starts out at an elevated temperature. And preheating also helps in thermal cutting of high thickness material.
How to determine Preheat Temperature
The exact preheating temperature and duration depend on various factors, including:\
Material Type: Different materials require different preheating temperatures. For instance, low-alloy steels generally require lower preheating temperatures than high-alloy steels.
Weld Thickness: Thicker sections typically require higher preheating temperatures to avoid cracking.
Ambient Conditions : The ambient temperature and humidity can influence preheating requirements. Humid and cold temperature generally required preheat in welding.
How to measure Preheat:
Preheat measuring often is done with Temperature indicating stick (tempilstik) and infrared digital thermometers. Generally, the preheat temperature should be measured for a distance at least equal to the thickness of the thickest welded part (but not less than 3 in [75 mm]) in all directions from the point of welding and be preferably measured on the opposite face to the one being welded.. The preheat temperature should be verified directly before welding begins.
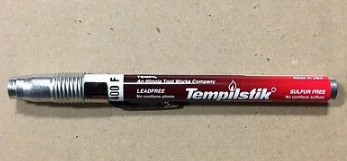
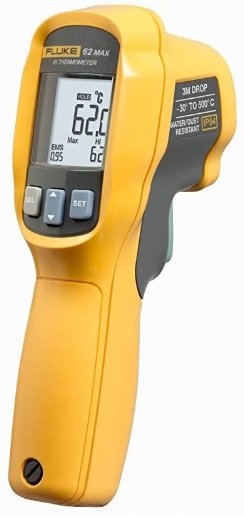
Preheat Requirements as per various codes and standards:
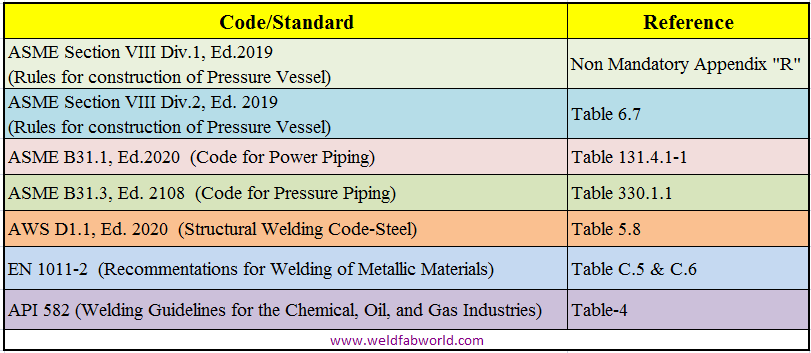
ASME Section IX Article Series
Very nice information