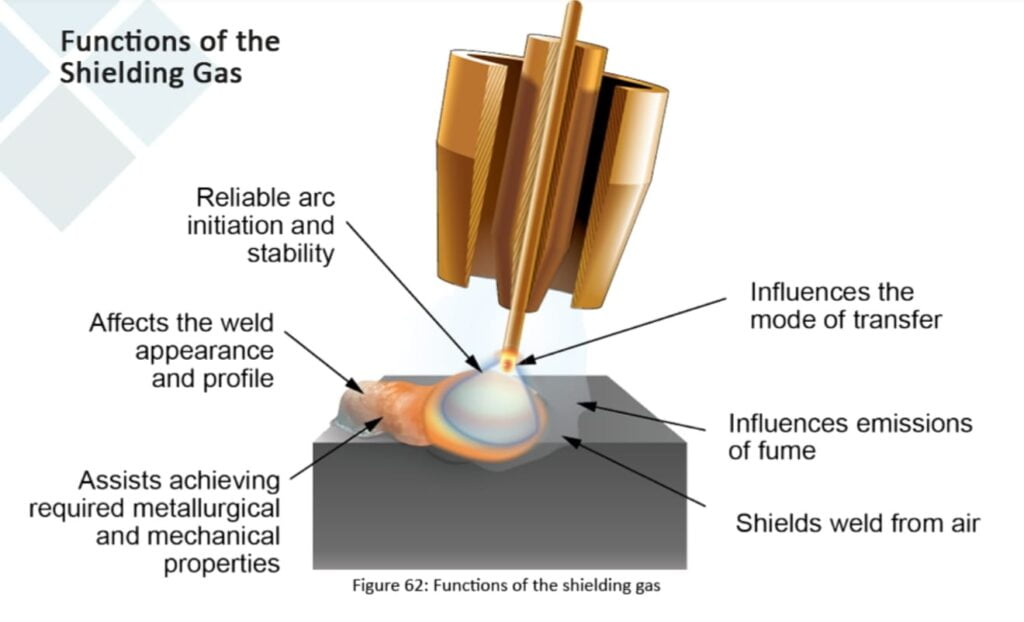
Welding is a fundamental process used across various industries to join metals permanently. Whether it’s for manufacturing structures, pipelines, automotive parts, or even artistic creations, welding plays a crucial role in shaping modern society. One essential aspect of welding is the use of shielding gases, which are employed to protect the welding area and the molten metal from harmful atmospheric elements. In this article, we will explore the reasons why shielding gases are required during welding and their role in ensuring high-quality welds.
Welding involves melting the edges of two metal pieces and fusing them together to create a strong, continuous bond. The heat generated during the welding process causes the metal to reach its melting point, creating a pool of molten metal. As the molten metal cools and solidifies, the two metal pieces become permanently joined.
During welding, the molten metal is exposed to the surrounding atmosphere, which typically consists of oxygen, nitrogen, and other gases. These gases can react with the molten metal and lead to several issues, including: oxidation, porosity, nitriding.
Shielding gases are used to prevent the exposure of weld pool to the atmospheric gases present in atmosphere. The reaction of atmospheric (basically oxygen and nitrogen) gases with the weld pool will damage (oxide formation) the weld.
Shielding gases are also helpful in achieving the metallurgical properties such as improved corrosion resistance and also (different gases impact different properties) helps to achieve improved mechanical properties such as tougher weld metal, ductility and strength.
Shielding gases may be inert or semi-inert gas. Shielding gases are being selected according to the material to be welded and process employed during welding.
How Shielding Gases Work
Shielding gases create a protective atmosphere around the welding area, preventing the harmful effects of atmospheric gases on the molten metal. They essentially displace the atmospheric gases, forming a barrier that isolates the weld from the surrounding air. Commonly used shielding gases include argon, helium, carbon dioxide, and mixtures of these gases.
The choice of shielding gas depends on the welding process, the type of metal being welded, and the desired weld characteristics. For instance, pure argon is often used for Tungsten Inert Gas (TIG) welding of non-ferrous metals, while carbon dioxide is commonly used in Metal Inert Gas (MIG) welding of steel.
Types of Shielding Gases:
Different gases being used for shielding for different welding processes. Gases are basically categorized on the basis of their chemical stability i.e. inert gases and semi-inert/active gases.
Inert Gases:
An inert gas is a gas which does not react with other gases under specified conditions. Commonly used inert gases for shielding of weld pool are argon and helium. Inert gases are useful, as they allow welds to be achieved naturally without unwanted occurrences weakening or distorting the weld.
Semi-Inert/Active Gases:
Unlike inert gases, semi-inert gases/active gases react with weld pool during welding. So these gases are used in small quantities to provide a positive change during the process of the weld, to enhance the weldability or to achieve better mechanical or metallurgical properties. Commonly used active gases are Carbon-dioxide, hydrogen, oxygen and nitrogen.
Benefits of Shielding Gases
Using shielding gases during welding offers several significant benefits, including:
A. Improved Weld Quality: By preventing oxidation, porosity, and nitriding, shielding gases help produce welds with higher integrity, strength, and reliability.
B. Cleaner Welds: Shielding gases minimize the formation of undesirable impurities in the weld, resulting in cleaner, visually appealing weld beads.
C. Greater Welding Control: The use of shielding gases allows welders to have better control over the welding process, leading to precise and accurate welds.
D. Reduced Post-Weld Cleanup: Since shielding gases minimize weld defects, there is less need for extensive post-weld cleanup and rework.
Common Shielding Gases Used in Welding and their Properties:
- Argon (Ar): Argon is a nonflammable, nontoxic, inert gas; and most commonly used for GTAW, PAW and MIG welding. Argon is used for shielding on most of ferrous and non-ferrous metal like carbon steel, stainless steel, aluminum, titanium and nickel, copper and magnesium alloys. Argon is used singularly and in combination with other gases to achieve desired arc characteristics for the welding of both ferrous and nonferrous metals. The low-ionization potential of argon creates an excellent current path and superior arc stability.
- Carbon Dioxide (CO2): CO2 is active gas; and most commonly used for GMAW and FCAW. The heat of the arc dissociates the carbon dioxide into carbon monoxide and free oxygen. This oxygen will combine with elements transferring across the arc and released from the weld poll in the form of slag and scale. Pure CO2 is used on Carbon and stainless steel metals for GMAW and FCAW process. Carbon dioxide can be used for solid electrode GMAW with short circuiting and globular transfer but not for spray transfer. CO2 is popular is due to common availability as well as its lower cost per unit volume.
- Nitrogen (N): Nitrogen is active gas; and shielding gases containing nitrogen are not recommended generally. Nitrogen will combine with other elements at higher temperature that is why not recommended as primary gas but used is used in combination with other gases for selected applications. Nitrogen is used as backing gas to protect the weld root from atmospheric contamination. Small additions (≤3%) of nitrogen have been combined with argon for GMAW and GTAW welding of duplex stainless steel. Increased nitrogen content of the weld may reduce the ferrite level.
- Helium: Helium is inert gas; it is used for weld application requires higher heat input. Helium may improve depth of fusion and travel speed. Helium has higher ionization potential so it produces hotter arc at higher voltage, provides wide deep bead; this is an advantage for aluminum, magnesium, and copper alloys welding. Helium is lighter than air so requires higher flow rates comparatively. Pure helium is not used for steel, as it causes an erratic arc and encourages spatter. It is generally used for GTAW welding.
- Oxygen: Oxygen is active gas; it can never be used as base component of shielding gas but added in small amounts to other gases; typically as 2–5% addition to argon. It enhances arc stability. Oxygen mixture with other also can only be used on carbon and stainless steel. Oxygen causes oxidation of the weld, so it is not suitable for welding aluminum, magnesium, copper, and some exotic metals. Oxygen mixture is used for GMAW and FCAW welding.
- Hydrogen: Hydrogen is flammable active gas; commonly used in low percentages (1 to 35%) as a minor component in a gas mixture. Its addition narrows the arc and increases the arc temperature, leading to better weld penetration. It is used on stainless steel and conductive materials like copper. However, it should not be used on steel, aluminum or magnesium because it can cause porosity and hydrogen embrittlement.
- Mixture Gases: Above stated gases can be used in welding different proportion for different welding application to achieve different properties, arc characteristics, and cleanliness of base metal, metal transfer mode and different penetration.
Factors to be Considered While Selecting Proper Shielding Gas
Proper gas selection is crucial to efficient welding in the most cost-effective manner. Many factors must be considered. These are not limited to the following:
- Type and thickness of base metal being welded
- Arc characteristics
- Metal transfer Mode
- Travel Speed
- Depth and Width of fusion
- Cost of welding
- Mechanical Properties
- Root opening
- Spatter
- Gas Purity
- Welding position
- Joint configuration
- Fume generation
Good Article. One can add the following points also.
Shielding gases help in two ways both primary as well as secondary functions
Protection from atmosphere you already mentioned.
One is shielding gas also helps in arc initiation and stabilizing the arc and helps in achieving bead characteristics.
Also can mention advantages & disadvantages of particular shielding gas
and shielding gases used for particular welding process.