This article differentiates between a welder and a welding operator, explores the purposes of their qualifications, and outlines how ASME Section IX categorizes welding into manual, semi-automatic, machine, and automatic welding
ASME Section IX provides the necessary guidelines for certifying personnel involved in welding activities. Section IX distinguishes between welders and welding operators and specifies criteria and factors for their qualification.
Purpose of Performance Qualification
The objective of welder Performance Qualification is to determine an individual’s capacity to create a sound joint using a material joining process.
When it comes to Operator Performance Qualification, the fundamental criterion is to determine the operator’s capability to operate the equipment correctly in order to create a sound joint.
Welder and Welding Operator Definition
What is a welder: One who is performing manual or semi-automatic welding is called a welder.
What is welding operator: One who operates a machine or automatic welding equipment is called a welding operator.
As previously explained, the classification of a person as either a welder or a welding operator depends on the welding technique in use. Therefore, in order to understand the distinction between a welder and a welding operator, it is essential to understand the differences among manual, semi-automatic, machine, and automatic welding techniques. Below, we have provided descriptions of these terms, with images for better understanding.
Difference Between Manual, Semi-automatic, Machine and Automatic Welding
Manual Welding: Manual welding is a welding method where all welding processes are manually controlled, including the manipulation of the electrode holder, welding torch and any additional filler by hand. This technique does not involve the use of mechanical devices to control these equipment. Examples of manual welding methods include SMAW (Shielded Metal Arc Welding) and manual GTAW (Gas Tungsten Arc Welding), as shown in the figure below.
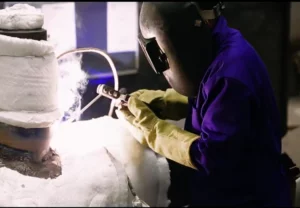
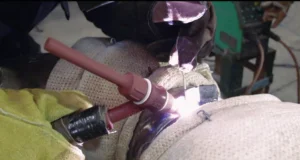
GTAW Manual Welding
Semiautomatic Welding: Semi-automatic welding is a method in which the equipment employed manages the delivery of filler metal, while the progression of the welding process is manually controlled. In this technique, a wire feeder is connected to the welding apparatus, which continuously feeds the filler metal through the welding torch. However, the torch itself is manually directed during the welding process. Examples of this welding method include FCAW (Flux-Cored Arc Welding), GMAW (Gas Metal Arc Welding), and GTAW (Gas Tungsten Arc Welding) with a wire feeder, as shown in the figure below.

Machine Welding: Machine welding is characterized by the use of equipment with controls that can be adjusted by the welding operator or modified under the direct supervision of the welding operator, in response to changes in welding conditions. In this method, a mechanical or electronic device holds the torch, gun, or electrode holder. Essentially, all welding operations are regulated by mechanical or electronic devices, with welding operators manually adjusting parameters as necessary to ensure the creation of a sound weld. Examples of this welding technique include SAW (Submerged Arc Welding), GMAW (Gas Metal Arc Welding), FCAW (Flux-Cored Arc Welding), and GTAW (Gas Tungsten Arc Welding) when the torch is mechanically held and the filler metal feed is electronically controlled. The image below illustrates the process of machine welding.
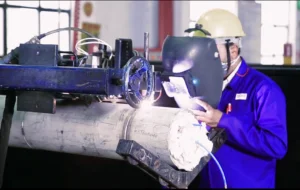
Automatic Welding: Automatic welding is characterized by the use of equipment that conducts welding operations without the need for manual control adjustments by a welding operator. In this technique, the welding operator doesn’t need to manipulate parameters during the welding process. Instead, a pre-established welding program is created before commencing the weld, where welding parameters are preset and executed automatically by the welding equipment throughout the process. A prime example of this type of welding is robotic welding, where a predefined program is stored prior to welding, and the operator simply initiates the program, with all welding activities carried out automatically. Loading and unloading processes may or may not be handled by the welding equipment. The image below illustrates the concept of automatic welding
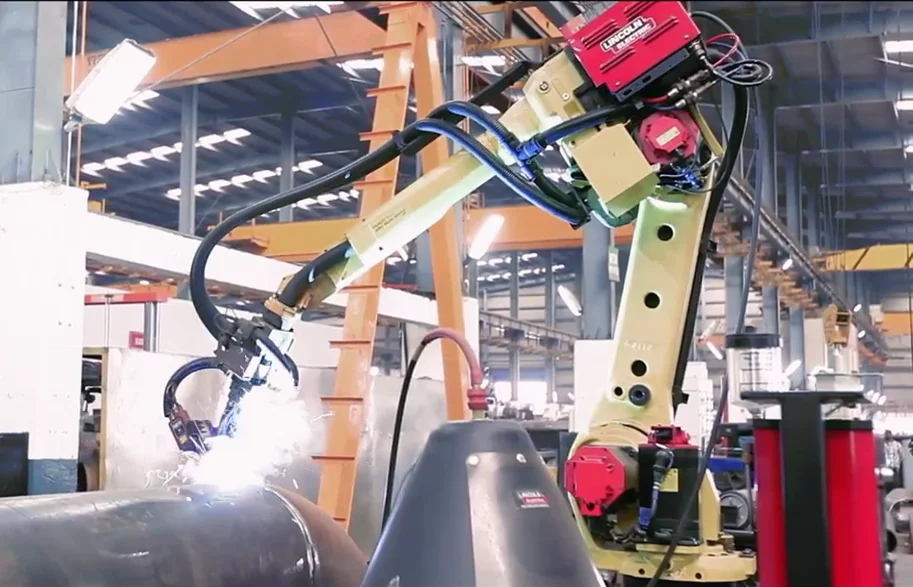
The provided definitions are sourced from ASME BPVC Section IX, AWS 3.0, and BS 499-1. To access the standardized definitions, you can refer to these codes.