Fractography is the study of fracture surfaces of materials, especially metals, to determine the causes and mechanisms of failure. This technique plays a pivotal role in metallurgy, materials science, and engineering failure investigations. By examining the surface of broken components using tools like Scanning Electron Microscopy (SEM) or low-magnification stereo-microscopy, engineers can uncover deep insights about failure mechanisms and root causes.
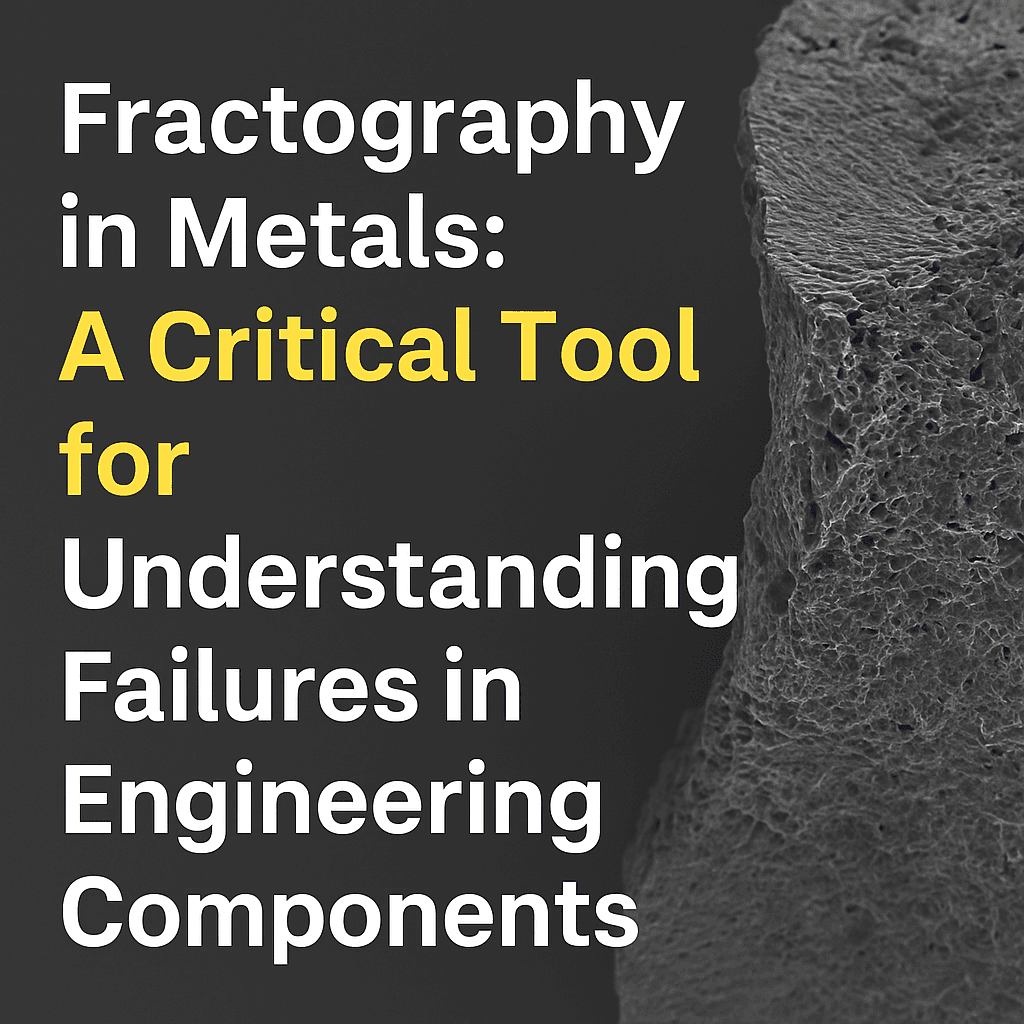
Importance of Fractography in Metallurgy and Failure Analysis
Fractography allows experts to identify:
– Root causes of failure
– Stress concentrations and their effects
– Internal and surface defects
– Influence of corrosion and environmental degradation
– Impact of manufacturing or heat treatment variations
Note: The skill and experience of the SEM operator plays a vital role in accurately identifying failure characteristics.
Fractography of Shafts: Focus on Fatigue Failures
Shafts are commonly used in mechanical systems and frequently experience fatigue failure due to cyclic loading. Understanding fatigue fracture mechanisms through fractography is essential for designing reliable and long-lasting shafts.
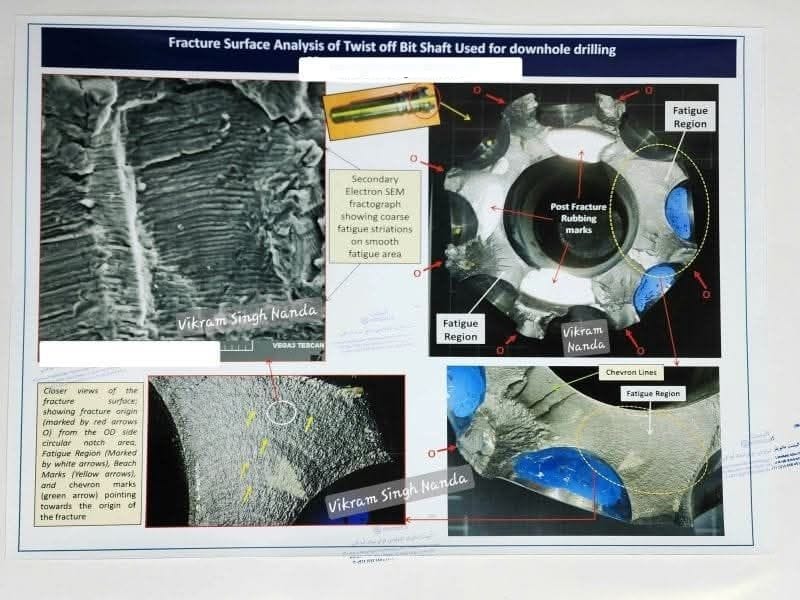
Fatigue Cracks
Fatigue cracks typically originate at the material surface, especially from areas with imperfections or high stress concentrations such as:
– Sharp corners
– Keyways
– Threads
– Machining marks or scratches
Crack Initiation Sites
Common initiation points for fatigue cracks include:
– Surface defects (scratches, pits)
– Corrosion marks
– Sharp fillet radii or sudden geometry changes
– Machining grooves or poor surface finishCrack Propagation
Fatigue cracks grow incrementally over time. Key visual indicators include:
– Striations (visible under SEM)
– Beach marks (visible at low magnification)
Eventually, the remaining material can no longer bear the load, leading to ductile overload failure.
Role of Material Properties
Fatigue resistance of a shaft depends on material characteristics such as:
– Fatigue strength
– Fracture toughness
– Microstructure (affected by heat treatment)
– Surface hardness and ductility
Fatigue Life and Operating Conditions
Fatigue life refers to the number of load cycles a shaft can endure before failure. Influencing factors include:
– Load magnitude and frequency
– Type of loading (axial, torsional, bending)
– Surface finish quality
– Operating environment (e.g., temperature, corrosion)
Environmental Factors
Environmental conditions can drastically reduce fatigue life:
– Temperature fluctuations
– Presence of moisture or corrosive chemicals
– UV exposure
– Abrasive dust or particles
These factors accelerate Fatigue Crack Growth Rate (FCGR) by interacting with the crack tip and weakening the material further.
Common Failure Modes in Shafts
Understanding different fatigue failure modes is essential for shaft design. Some common types include:
– Low Cycle Fatigue (LCF)
– High Cycle Fatigue (HCF)
– Surface or Contact Fatigue
– Fretting Fatigue
– Corrosion Fatigue
– Environmentally Assisted Fatigue Cracking (EAFC)
Conclusion
Fractography is a powerful diagnostic tool in mechanical and materials engineering. By analyzing fracture surfaces in detail, engineers and failure analysts can discover the real reasons behind material breakdowns. This knowledge is critical for:
– Improving shaft designs
– Selecting appropriate materials
– Enhancing reliability
– Reducing costly downtime
Follow WeldFabWorld for More Technical Insights
Stay updated with the latest knowledge in welding, fabrication, materials science, and mechanical engineering:
🌐 Website: WeldFabWorld.com
📸 Instagram: @weldfabworld
🎥 YouTube: WeldFabWorld Channel
🐦 X (Twitter): @Weldfabworld
📢 Telegram: WeldFabWorld Telegram
📲 WhatsApp Channel: Join Here