Magnetic Particle Inspection (MPI) stands as a crucial nondestructive testing process utilized to detect surface and shallow subsurface discontinuities in ferromagnetic materials. These materials encompass iron, nickel, cobalt, and certain alloys susceptible to magnetization. The method involves establishing a magnetic field within the test object, achieved through direct or indirect magnetization. Direct magnetization passes electric current through the test object, forming a magnetic field within the material. In contrast, indirect magnetization applies a magnetic field externally without passing electric current through the test object. This process induces a condition where any presence of surface or subsurface discontinuity allows magnetic flux to leak, attracting ferrous particles—either dry or suspended in a wet medium—to form an indication. This indication is then assessed to determine its nature, cause, and necessary action.
Electrical Current Variants
Several electrical currents are employed in magnetic particle inspection, selected based on considerations like part geometry, material, desired discontinuity type, and required magnetic field penetration depth.
- Alternating current (AC): Primarily used to detect surface discontinuities due to its limited penetration depth caused by the skin effect—a phenomenon where the current runs along the part’s surface. The frequency of AC determines its depth of penetration.
- Full wave DC: Utilized to detect subsurface discontinuities beyond the reach of AC. The depth of penetration depends on the current passing through the part.
- Half wave DC (HWDC, pulsating DC): Similar to full wave DC but offers enhanced mobility of magnetic particles, aiding in detecting surface-breaking indications and penetrating the part more effectively than full wave DC.
- AC electromagnet: Preferred for finding surface-breaking indications. However, detecting subsurface indications with an AC electromagnet poses challenges.
Steps of Magnetic Particle Inspection
Magnetization:
The first step in MPI is to magnetize the test specimen. This is done by either using a magnetic yoke, a permanent magnet, or an electromagnet. The magnetization induces a magnetic field in the material being tested.
Application of Magnetic Particles:
Magnetic particles in the form of a dry powder or a wet suspension (containing finely divided iron or iron oxide particles) are applied to the surface of the material. These particles are typically colored with a fluorescent or contrasting dye for better visibility.
Inspection Under Ultraviolet (UV) or White Light:
The magnetized part is inspected under ultraviolet (UV) light or white light, depending on the type of magnetic particles used. UV light is often used when fluorescent particles are applied. The presence of a magnetic field causes the magnetic particles to align along the lines of magnetic flux, creating a visible indication at the location of a defect.
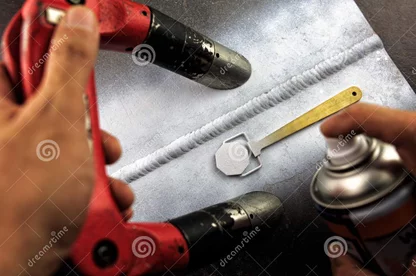
Indication Interpretation:
Trained inspectors examine the surface for indications, which appear as lines or clusters of magnetic particles. These indications are called “magnetic particle indications” or “magnetic indications.” The size, shape, and location of these indications are analyzed to determine their significance and whether they meet specified acceptance criteria.
Demagnetization:
After the inspection is complete, the test specimen is usually demagnetized to remove any residual magnetism. This can be done using techniques like AC demagnetization or decreasing the magnetic field gradually.
Reporting:
The results of the Magnetic Particle Inspection are documented in a report, which includes information about the inspection process, the location and characteristics of any indications found, and the disposition of each indication (acceptable or reject).
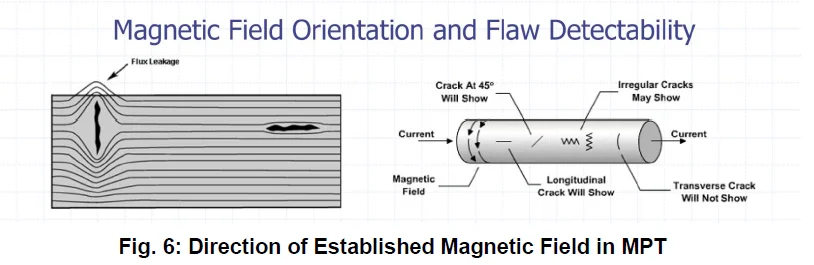
Advantages & Limitations of Magnetic Particle Inspection
Criteria | Advantages of MPI | Limitations of MPI |
---|---|---|
Defect Detection | Can find both surface and near sub-surface defects | The specimen must be ferromagnetic (e.g., steel, cast iron) |
Portability and Cost | Some formats are extremely portable and low cost | Paint thicker than about 0.005″ must be removed before inspection |
Speed and Immediate Results | Rapid inspection with immediate results | Post cleaning and post demagnetization are often necessary |
Visibility of Indications | Indications are visible to the inspector directly on the specimen surface | Maximum depth sensitivity is typically quoted as 0.100″ (deeper under perfect conditions) |
Defect Detection Capability | Can detect defects that have been smeared over | Alignment between magnetic flux and defect is important |
Versatility in Part Shapes | Can inspect parts with irregular shapes (external splines, crankshafts, connecting rods, etc.) | – |
Magnetic Particle Inspection is commonly used in industries such as aerospace, automotive, construction, and manufacturing to detect surface and near-surface defects in materials, particularly in welds, castings, forgings, and other critical components made of ferromagnetic materials. It is a relatively quick and cost-effective NDT method, making it suitable for production line testing and field inspections. Proper training and adherence to industry standards are essential for the accurate and reliable application of MPI.
Standards
Standards International Organization for Standardization (ISO)
- ISO 3059, Non-destructive testing – Penetrant testing and magnetic particle testing – Viewing conditions
- ISO 9934-1, Non-destructive testing – Magnetic particle testing – Part 1.. General principles
- ISO 9934-2, Non-destructive testing – Magnetic particle testing – Part 2.. Detection media
- ISO 9934-3, Non-destructive testing – Magnetic particle testing – Part 3.. Equipment
- ISO 17638, Non-destructive testing of welds – Magnetic particle testing
- ISO 23279, Non-destructive testing of welds – Magnetic particle testing of welds – Acceptance levels
European Committee for Standardization (CEN)
- EN 1290, Surface Crack Testing
- EN 1330-7, Non-destructive testing – Terminology – Part 7.. Terms used in magnetic particle testing
- EN 1369, Founding – Magnetic particle inspection
- N 10228-1, Non-destructive testing of steel forgings – Part 1.. Magnetic particle inspection
- EN 10246-12, Non-destructive testing of steel tubes – Part 12.. Magnetic particle inspection of seamless and welded ferromagnetic steel tubes for the detection of surface imperfections
- EN 10246-18, Non-destructive testing of steel tubes – Part 18.. Magnetic particle inspection of the tube ends of seamless and welded ferromagnetic steel tubes for the detection of laminar imperfections
American Society of Testing and Materials (ASTM)
- ASTM E1444-05
- ASTM A 275/A 275M Test Method for Magnetic Particle Examination of Steel Forgings
- ASTM A456 Specification for Magnetic Particle Inspection of Large Crankshaft Forgings
- ASTM E543 Practice Standard Specification for Evaluating Agencies that Performing Nondestructive Testing
- ASTM E 709 Guide for Magnetic Particle Testing Examination
- ASTM E 1316 Terminology for Nondestructive Examinations
- ASTM E 2297 Standard Guide for Use of UV-A and Visible Light source and Meters used in the Liquid Penetrant and Magnetic Particle Methods