To ensure the satisfactory performance of a component/structure, the component shall be tested with adequate testing procedure with the adequate testing method. Which in general specifies component can be used in the service requirement specified. Soundness to the purpose of component can be determined by either destructive or non-destructive testing of the component. But as destructive testing caused permanent damage to the product it cannot be done on the final products to be utilized in the service. So that component shall be tested with the non-destructive testing methods.
NDT refers to the non-destructive testing. NDT is an approach in which products are evaluated without causing damage to the component and can serve the desired purpose after testing. With NDT industries evaluates the properties of material, component without damaging them. As NDT does not alter the properties of the component it is technique which can save money and time both. We will discuss different types of non-destructive testing in this article.
Types of Non-destructive testing: Many Non-destructive testing methods are developed to evaluate the soundness of material and many are being developed to test the components in which if failure occurs can cause severe damage like welded components, pressure vessels, bridges etc. Some of most common methods are categorized below
Visual Examination (VT)
Visual testing of welds is a crucial part of quality control in welding processes. It involves visually inspecting welded joints to identify surface imperfections, discontinuities, and other defects that may affect the structural integrity of the weld. Visual testing is often the first and most basic method used in weld inspection and is typically performed by certified welding inspectors (CWIs) or qualified personnel with the necessary training and expertise.
Visual defects in welding can compromise the integrity and quality of the welded joint. Welding inspectors and technicians are trained to identify these defects during visual inspections. Here is a list of common visual defects in welding:
- Incomplete Fusion
- Lack of Penetration
- Undercut:
- Overlap
- Porosity
- Cracks
- Inclusions
- Excessive Reinforcement
- Underfill
- Spatter
- Burn-Through
- Inadequate Weld Size
- Excessive Weld Reinforcement
- Surface Contaminants
It’s essential for welding inspectors and personnel involved in welding to be well-trained in recognizing these defects to ensure the safety and reliability of welded structures and components. Welding standards and codes typically provide guidelines for acceptable defect limits and quality requirements in various applications.
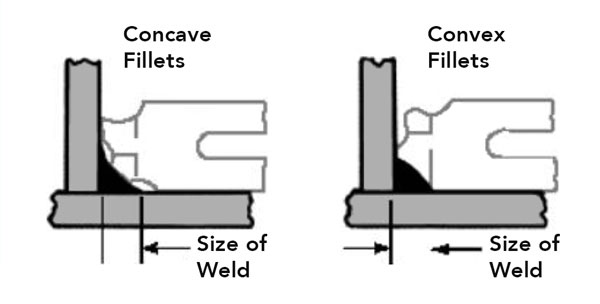
Dye Penetration Test (DPT)
Dye Penetrant Testing (DPT), also known as Liquid Penetrant Testing (LPT) or Penetrant Inspection (PI), is a nondestructive testing (NDT) method used to detect surface defects, cracks, and discontinuities in materials, especially in metals, plastics, ceramics, and composites. It’s a widely used method for quality control and defect detection in various industries, including aerospace, automotive, manufacturing, and construction.
Here’s an overview of the Dye Penetrant Testing method:
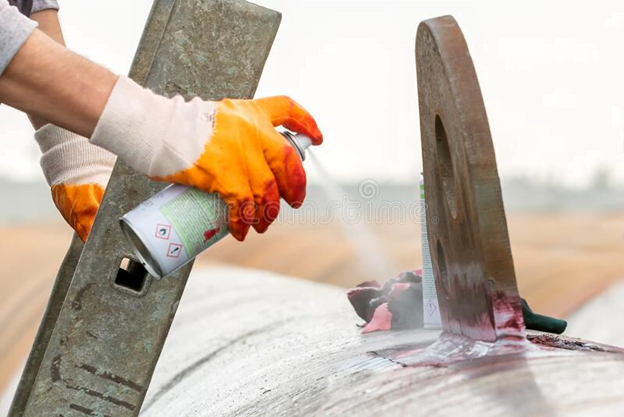
Dye Penetrant Testing (DPT)
- Surface Preparation:
- The first step is to thoroughly clean the surface of the material being tested. Any contaminants like dirt, grease, oil, or rust must be removed because they can interfere with the test results.
- Application of Penetrant:
- A liquid penetrant, often a brightly colored dye, is applied to the cleaned surface. The penetrant is allowed to soak into any surface openings or defects through capillary action. This usually involves spraying, brushing, or immersion methods.
- Dwell Time:
- The penetrant is left on the surface for a specified period known as the “dwell time.” During this time, it seeps into any surface discontinuities and fills them.
- Excess Penetrant Removal:
- After the dwell time, excess penetrant is removed from the surface. This is typically done using a solvent cleaner or by simply wiping the surface.
- Application of Developer:
- A white, powdery developer is applied to the surface. The developer helps to draw out any penetrant material that is trapped in surface defects and makes them visible.
- Development Time:
- The developer is allowed to sit on the surface for a specified period called the “development time.” During this time, any trapped penetrant material will migrate to the surface and create visible indications.
- Inspection:
- Trained inspectors visually examine the surface for indications. These indications appear as bright, colored lines or spots against the white developer background. The size, shape, and location of the indications are carefully evaluated.
- Evaluation:
- Inspectors assess the indications to determine their significance. Not all indications are necessarily defects; they might be acceptable imperfections depending on the inspection criteria and industry standards.
- Reporting:
- The results of the Dye Penetrant Testing are documented in a report, which includes information about the inspection process, the location and characteristics of any indications found, and the disposition of each indication (acceptable or reject).
Dye Penetrant Testing is a relatively simple and cost-effective NDT method for detecting surface defects and discontinuities. However, it is limited to detecting defects that are open to the surface and may not detect subsurface defects. It is essential to follow industry-specific standards and procedures to ensure the reliability and accuracy of the inspection results.
Radiographic examination (RT)
Radiographic Testing (RT), also known as Industrial Radiography or X-ray Inspection, is a nondestructive testing (NDT) method used to examine the internal structure of materials, especially metals and welds, for defects and anomalies. It relies on the use of ionizing radiation, such as X-rays or gamma rays, to create images of the object’s interior. Here’s how Radiographic Testing is typically conducted:
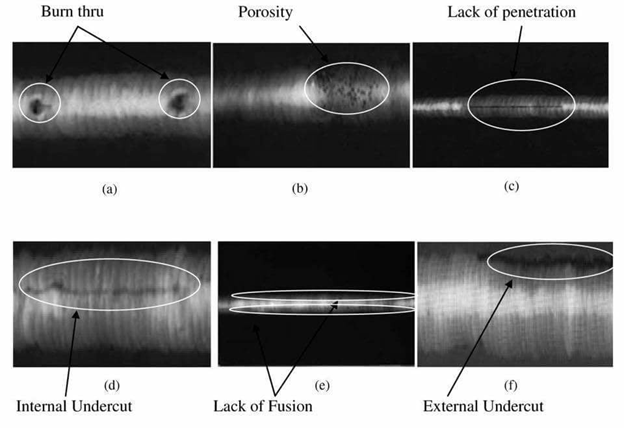
Defects in Radiographic Testing (RT)
- Radiographic Equipment Setup:
- A radiographic source is placed on one side of the object being tested, and a radiographic film or digital detector is placed on the opposite side. The object is positioned between these two components. The source emits ionizing radiation, which penetrates the material and interacts with it.
- Exposure:
- The ionizing radiation passes through the material and interacts differently with various materials and defects. Dense materials, such as welds or internal discontinuities, absorb more radiation and appear as darker areas on the radiographic image, while less dense areas allow more radiation to pass through and appear as lighter areas.
- Radiographic Image Formation:
- The radiation that passes through the material exposes the radiographic film or digital detector. In traditional film radiography, the exposed film is developed to produce a visible image. In digital radiography, a digital image is directly generated and can be immediately viewed and analyzed on a computer.
- Image Interpretation:
- Trained radiographers and inspectors examine the radiographic images for indications of defects, such as cracks, voids, porosity, inclusions, or other anomalies. The size, shape, and location of these indications are carefully analyzed to determine their significance and whether they meet specified acceptance criteria.
- Reporting:
- The results of the Radiographic Testing are documented in a report, which includes information about the inspection process, the location and characteristics of any indications found, and the disposition of each indication (acceptable or reject).
Radiographic Testing is a powerful NDT method for detecting both surface and subsurface defects, making it suitable for applications where hidden internal flaws could compromise the structural integrity of the material or component. It is commonly used in industries such as aerospace, construction, manufacturing, and oil and gas.
However, Radiographic Testing involves the use of ionizing radiation, which can be hazardous to personnel and requires strict safety measures and regulatory compliance. Radiographers must be trained and certified to ensure the safe operation of radiographic equipment and the protection of workers and the environment.
Magnetic Particle Inspection (MPI)
Magnetic Particle Inspection (MPI), also known as Magnetic Testing (MT) or Magnetoscopic Testing, is a widely used nondestructive testing (NDT) method for detecting surface and near-surface defects in ferromagnetic materials. Ferromagnetic materials include iron, steel, nickel, and cobalt, among others. MPI relies on the magnetic properties of these materials to identify flaws such as cracks, weld defects, and other discontinuities.
Here’s an overview of how Magnetic Particle Inspection is typically conducted:
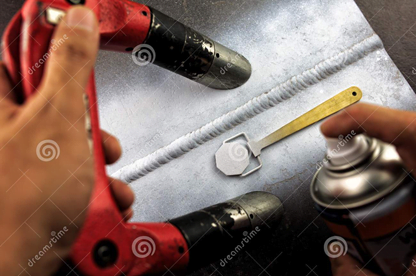
Magnetic Particle Inspection (MPI)
Magnetic Particle Inspection is performed in four steps..
- Induce a magnetic field in the specimen
- Apply magnetic particles to the specimen’s surface
- View the surface, looking for particle groupings that are caused by defects
- Demagnetize and clean the specimen
Magnetic Particle Inspection is commonly used in industries such as aerospace, automotive, construction, and manufacturing to detect surface and near-surface defects in materials, particularly in welds, castings, forgings, and other critical components made of ferromagnetic materials. It is a relatively quick and cost-effective NDT method, making it suitable for production line testing and field inspections. Proper training and adherence to industry standards are essential for the accurate and reliable application of MPI.
For complete article visit on MPI
Ultrasonic examination (UT)
Ultrasonic Examination of Welds (UT) is a nondestructive testing (NDT) method that uses high-frequency sound waves (ultrasound) to detect and characterize weld defects and discontinuities in various materials, particularly metals and alloys. UT is widely used in industries such as manufacturing, construction, aerospace, and petrochemical to ensure the integrity of welded joints and to verify compliance with quality standards. Here’s an overview of how Ultrasonic Examination of Welds is typically conducted:
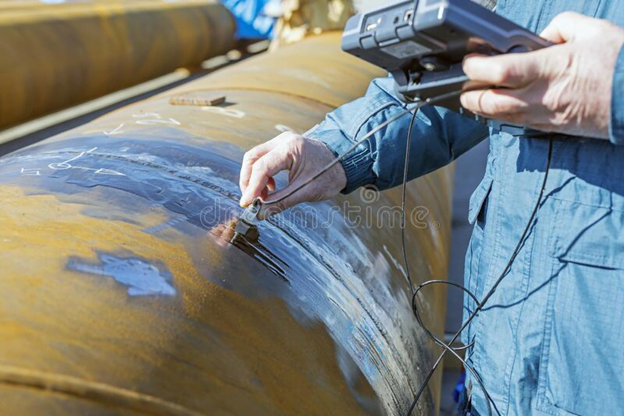
Ultrasonic examination (UT)
- Ultrasonic Equipment Setup:
- An ultrasonic testing instrument, often called an ultrasonic flaw detector, is used for this examination. The instrument generates high-frequency sound waves (typically in the range of 0.5 to 25 MHz) and sends them into the material through a transducer (a probe). The transducer contains a piezoelectric crystal that converts electrical energy into mechanical vibrations (ultrasonic waves) and vice versa.
- Couplant Application:
- A couplant (usually a gel, oil, or water) is applied to the surface of the material being tested. This couplant ensures good acoustic coupling between the transducer and the material, allowing the ultrasonic waves to penetrate into the material effectively.
- Sound Wave Propagation:
- The ultrasonic waves are introduced into the material through the transducer. They travel through the material until they encounter a boundary or a defect. When the sound waves encounter a boundary (e.g., the opposite side of the weld), some of the energy is reflected back to the transducer, while the rest continues to propagate through the material.
- Echo Reception:
- The transducer also acts as a receiver and detects the echoes of the sound waves that are reflected back from internal boundaries or defects within the material. These echoes are displayed on the ultrasonic flaw detector’s screen as a series of peaks and valleys.
- Signal Analysis:
- The technician or inspector analyzes the ultrasonic signals for various characteristics, such as the amplitude, time of flight, and signal shape. Discontinuities within the material, such as cracks, voids, lack of fusion, and porosity, can create echoes or indications that appear on the display.
- Interpretation and Evaluation:
- The inspector interprets the ultrasonic signals to determine the size, location, and nature of any detected indications. This evaluation helps assess whether the weld meets specified acceptance criteria and standards.
- Reporting:
- The results of the Ultrasonic Examination of Welds are documented in a report, which includes information about the inspection process, the location and characteristics of any indications found, and the disposition of each indication (acceptable or reject).
Ultrasonic Examination of Welds is a powerful NDT method because it can detect both surface and subsurface defects and provides valuable information about the size and location of these defects. It is highly effective in assessing the quality of welded joints and ensuring structural integrity. Proper training and certification of technicians are crucial to obtaining accurate and reliable results in UT inspections.
Electromagnetic Testing/Eddy Current Testing (ECT):
Electromagnetic Testing (ET) is a nondestructive testing (NDT) method used to inspect welds and other metallic components for various defects and anomalies. ET relies on the principles of electromagnetic induction and changes in electrical conductivity to detect surface and subsurface flaws, such as cracks, inclusions, and discontinuities, in conductive materials, including metals. One common form of ET used for inspecting welds is Eddy Current Testing (ECT). Here’s an overview of Electromagnetic Testing with a focus on Eddy Current Testing of welds:
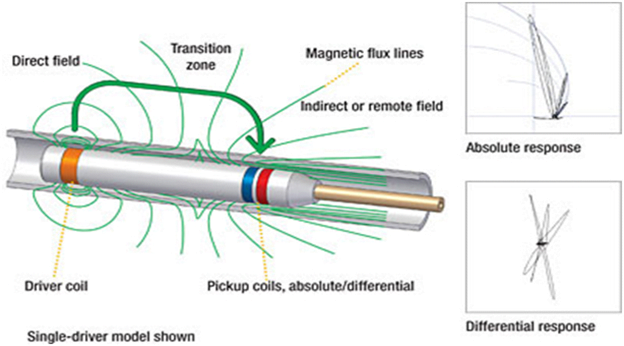
Eddy Current Testing (ECT):
- Principle of ECT:
- ECT works based on the principle of electromagnetic induction. When an alternating current (AC) is passed through a coil or probe, it generates changing magnetic fields around it. When this probe is placed near a conductive material, such as a metal weld, eddy currents are induced in the material. Any variations in the material’s electrical conductivity, caused by defects or anomalies, will disrupt the eddy currents, leading to measurable changes in the electrical response of the coil.
- Equipment Setup:
- ECT equipment typically includes a coil or probe, a drive system for moving the probe over the weld surface, and a receiver or impedance analyzer. The coil or probe is positioned close to the weld surface, and it generates the alternating magnetic field.
- Scanning Process:
- During the inspection, the coil or probe is scanned along the surface of the weld at a controlled speed. As it moves, it emits alternating magnetic fields and measures the electrical response, which is influenced by the material’s conductivity and any defects present.
- Signal Analysis:
- The ECT instrument analyzes the signals received from the coil or probe. Changes in the signals, such as shifts in phase, amplitude, or frequency, can indicate the presence of defects. The location and characteristics of these changes provide information about the size, shape, and depth of the anomalies.
- Interpretation and Evaluation:
- A trained inspector interprets the data to assess the weld’s condition. The inspector evaluates the indications detected and determines whether they meet specified acceptance criteria and industry standards.
- Reporting:
- The results of the Electromagnetic Testing (ECT) of welds are documented in a report, which includes information about the inspection process, the location and characteristics of any indications found, and the disposition of each indication (acceptable or reject).
Electromagnetic Testing, particularly Eddy Current Testing, is valued for its ability to quickly detect surface and subsurface defects in conductive materials like welds. It is a versatile NDT method suitable for various applications, including the inspection of aerospace components, automotive parts, and structural welds in construction. Proper training and experience are essential for conducting ET effectively and accurately interpreting the results.
Positive Material Identification (PMI)
Positive Material Identification (PMI) is a non-destructive testing (NDT) technique used to determine and verify the composition of materials, especially in welds and other critical components. PMI is crucial in ensuring that the correct materials have been used, which is vital for safety and compliance with industry standards and specifications. In the context of welds, PMI is essential for confirming that the base materials and filler metals are consistent with the specified requirements.
Here’s how PMI of welds is typically conducted:
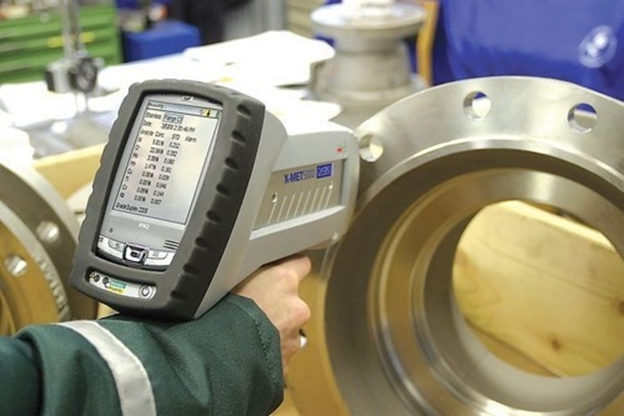
Positive Material Identification (PMI)
- Selection of PMI Equipment:
- PMI is typically performed using handheld or portable devices called PMI analyzers. These analyzers utilize various techniques, such as X-ray fluorescence (XRF), optical emission spectroscopy (OES), or laser-induced breakdown spectroscopy (LIBS), to determine the chemical composition of the material.
- Surface Preparation:
- Prior to analysis, the surface of the weld or the test location is prepared by cleaning it to remove any contaminants or surface oxidation that might affect the accuracy of the PMI readings.
- Calibration and Verification:
- The PMI analyzer is calibrated and verified to ensure its accuracy. This may involve testing reference samples with known compositions to verify that the instrument provides reliable results.
- Measurement:
- The PMI analyzer is placed in contact with the test material or weld, and a measurement is taken. Depending on the analyzer technology, it may use X-rays, a spark discharge, laser pulses, or other methods to analyze the material’s composition.
- Data Analysis:
- The PMI analyzer provides immediate results, displaying the chemical composition of the material being tested. These results are typically compared to the specified requirements or standards to verify compliance.
- Documentation:
- The PMI results are documented in a report, including details about the test, the location of the analysis, the chemical composition, and whether the material meets the specified requirements. This documentation is essential for quality control, record-keeping, and traceability.
PMI of welds is particularly important in industries such as oil and gas, petrochemical, aerospace, and manufacturing, where the use of correct materials and weld specifications is critical for safety and product reliability. By ensuring that the materials used in welds are consistent with the required standards, PMI helps prevent issues like corrosion, weld failures, and other structural problems.
It’s essential to use PMI equipment that is suitable for the type of material being tested and to have trained personnel who can operate the equipment correctly and interpret the results accurately.
Hardness testing
Hardness testing is a non-destructive or destructive testing method used to assess the hardness or resistance to deformation of a material. Hardness is an essential material property that can provide insights into its mechanical strength, wear resistance, and suitability for various applications. There are several methods for measuring hardness, with the most common being:
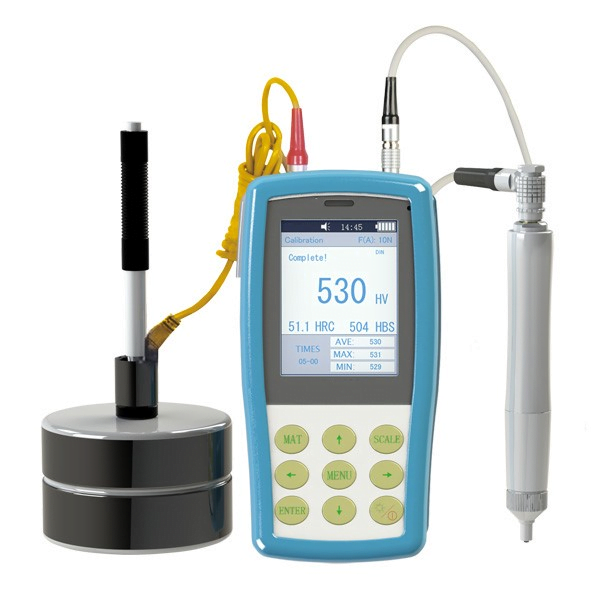
- Rockwell Hardness Test:
- The Rockwell hardness test involves applying a known load to an indenter (a diamond or tungsten carbide ball) and measuring the depth of penetration into the material. There are different scales within the Rockwell test method (e.g., HRC for hard materials and HRB for soft materials) based on the type of indenter and the applied load. The hardness value is represented as an H number, such as HRC 50.
- Brinell Hardness Test:
- In the Brinell hardness test, a hardened steel or tungsten carbide ball of a known diameter is pressed into the material under a known load. The resulting indentation is measured, and the hardness is calculated as the load divided by the surface area of the indentation. It is expressed as a Brinell hardness number (BHN), such as BHN 300.
- Vickers Hardness Test:
- The Vickers hardness test uses a diamond-shaped indenter with a specific geometry (usually a square-based pyramid) and applies a load to the material. The size of the indentation left behind is measured, and the hardness is calculated based on the load and the area of the indentation. The hardness value is expressed in Vickers hardness units (HV), such as HV 200.
- Knoop Hardness Test:
- The Knoop hardness test is similar to the Vickers test but uses a rhombic-based pyramidal diamond indenter. It is commonly used for testing brittle materials or thin sections. The hardness value is expressed in Knoop hardness units (HK), such as HK 100.
- Shore Hardness Test:
- Shore hardness, also known as durometer hardness, is primarily used for measuring the hardness of polymers, elastomers, and other soft materials. It uses a sharp-pointed indenter and measures the depth of penetration under a specific load. Shore hardness values are represented as Shore A, Shore D, etc.
- Microhardness Test:
- Microhardness testing is a subset of hardness testing that is performed at very small scales, often using Vickers or Knoop indenters. It is commonly used to assess localized hardness variations or very thin materials.
Hardness testing is widely used in various industries, including manufacturing, engineering, and materials science, to ensure the quality and consistency of materials and to determine their suitability for specific applications. Different materials and applications may require different hardness testing methods, and the choice of method depends on factors such as the material type, thickness, and the required accuracy of the hardness measurement.
Advantages of Non Destructive Testing:
- The properties of the component are not affected by the testing so can be used for the purpose.
- Product can be tested in actual condition no sample preparation required as of destructive testing.
- Setup cost is comparatively less.
- Economical than the destructive testing.
- NDT is reliable as gives the repeatable results and can be retested for conformance.
- NDT can be done at after working or during working which gives the actual condition of the product and measures can be taken for life extension of product.