In the world of non-destructive testing (NDT), dye penetrant testing is a widely employed method for detecting surface-breaking defects in various materials, including metals, plastics, and ceramics. This technique, often referred to as liquid penetrant inspection or simply penetrant testing, plays a crucial role in ensuring the structural integrity and safety of a wide range of products, from aircraft components to pipelines. In this article, we will delve into complexity of dye penetrant testing and explore the sequence of actions when performing this invaluable inspection process.
Understanding Dye Penetrant Testing
Dye Penetrant Testing works through capillary action, where a thin, low-surface-tension liquid enters into clean and dry surface defects. This liquid can be applied to the test object by dipping, spraying, or brushing. After giving it enough time to seep into the material, any extra liquid is wiped away, and then a developer is added. The developer’s job is to pull the liquid out of the flaws, making hidden defects visible to the inspector. To check for these defects, inspectors use either ultraviolet or white light, depending on the type of dye they’ve used – fluorescent or non-fluorescent (visible).
Sequence of Actions When Performing Penetrant Testing
1. Pre-cleaning:
Before conducting the test, the surface is thoroughly cleaned to get rid of dirt, paint, oil, grease, or loose scale. These substances could either block the penetrant from entering a defect or create misleading results. Cleaning methods may involve using solvents, alkaline cleaning solutions, vapor degreasing, or media blasting. The ultimate aim of this step is to have a pristine surface where any existing defects are exposed, dry, and free from any impurities. It’s worth noting that if media blasting is employed, it may slightly affect small irregularities in the part, and it’s advised to follow up with an etching bath treatment after blasting.
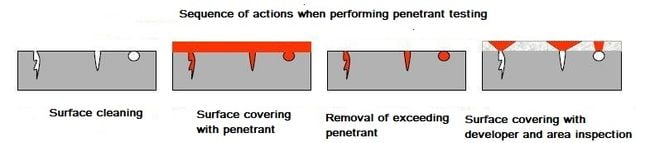
2. Application of Penetrant:
The penetrant is then applied to the surface of the item being tested. This penetrant is typically a bright colored, flowing liquid with a strong ability to spread out. It’s given a specific amount of time, known as the “dwell time,” to seep into any potential flaws, typically ranging from 5 to 30 minutes. The exact duration of the dwell time depends on factors like the type of penetrant used, the material being tested, and the size of the flaws being sought.
It’s important to note that smaller flaws require a longer time for the penetrant to fully penetrate. Additionally, one should be cautious not to apply a solvent-based penetrant to a surface that will be inspected with a water-washable developer, as they are not compatible.
3. Excess Penetrant Removal
After that, any extra penetrant is taken off from the surface. The method for removal depends on the type of penetrant used. There are commonly four options: water-washable, solvent-removable, lipophilic post-emulsifiable, or hydrophilic post-emulsifiable. Emulsifiers offer the highest level of sensitivity as they chemically interact with the oily penetrant, making it washable with water spray.
When using a solvent remover and a lint-free cloth, it’s essential not to spray the solvent directly onto the test surface because this can remove the penetrant from the flaws. If excess penetrant isn’t properly removed, it can create a background on the developed area, which might hide indications or defects and lead to inaccurate results. Moreover, this incomplete removal can generate false indications, making it difficult to conduct a thorough inspection. It’s also crucial to remove excessive penetrant in a consistent direction, either vertically or horizontally, depending on the situation.
4. Application of Developer:
Once the excess penetrant has been taken off, a white developer is spread over the sample. There are various developer types to choose from, such as non-aqueous wet developer, dry powder, water-suspendable, and water-soluble. The choice of developer depends on the compatibility with the penetrant used, and the specific inspection conditions. For instance, you can’t use water-soluble or water-suspendable developer with water-washable penetrant.
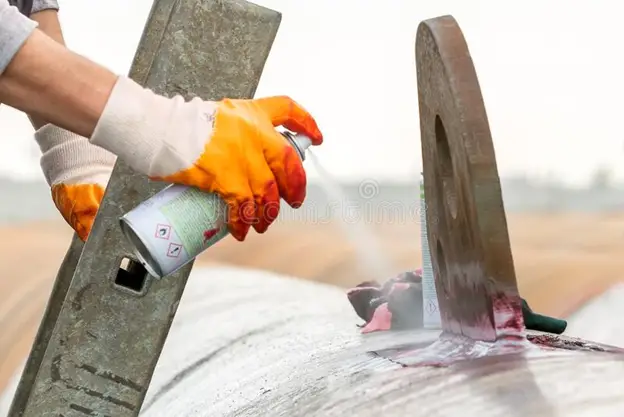
When using non-aqueous wet developer or dry powder, the sample needs to be dried before applying it, while soluble and suspendable developers are applied when the part is still wet from the previous step. Non-aqueous wet developer is often available in aerosol spray cans and may contain acetone, isopropyl alcohol, or a combination of both as a propellant. The developer should create a semi-transparent, even layer on the surface.
The developer’s role is to pull the penetrant from defects out onto the surface, forming visible indications, often referred to as bleed-out. These areas that bleed out can provide information about the location, orientation, and potential types of defects on the surface. Interpreting the results and characterizing defects based on these indications may require some training and experience, as the size of the indication doesn’t necessarily match the actual size of the defect.
5. Inspection:
The inspector will use suitable lighting, which typically involves using visible light with ample brightness (around 100 foot-candles or 1100 lux) for visible dye penetrant tests. In the case of fluorescent penetrant examinations, ultraviolet (UV-A) radiation with adequate intensity (usually around 1,000 micro-watts per centimeter squared) is utilized, along with keeping the surrounding light at low levels (less than 2 foot-candles).
The inspection of the test surface should occur after a development period lasting between 10 to 30 minutes, depending on the specific penetrant and developer combination used. This waiting period allows for the bleed-out action to take place, which is essential for forming indications. When employing visible dye, the inspector may watch the sample to observe how indications develop. It’s considered good practice to monitor these indications as they form, as the characteristics of the bleed-out are a significant part of interpreting and characterizing defects.
6. Post Cleaning:
After inspection, the remaining penetrant material and developer are removed from the part. This ensures the part’s cleanliness and prevents potential contamination in the future.
Dye penetrant testing is a versatile method that can be tailored to specific inspection needs. It can be used on a wide range of materials and is an efficient way to detect surface defects in various industries, from manufacturing to aviation. When executed with precision and adherence to the established sequence of actions, dye penetrant testing is a powerful tool for quality control and safety assurance.
In conclusion, dye penetrant testing is a valuable asset in the arsenal of non-destructive testing techniques. By following a well-defined sequence of actions, technicians can unlock hidden flaws in materials, ensuring the reliability and safety of critical components in countless applications. The careful execution of each step, from pre-cleaning to post-cleaning, is essential for the success of this method and the continued integrity of the materials under examination.