Welding is a critical process in numerous industries, from construction to automotive manufacturing. One of the key factors in achieving a successful weld is understanding the concept of polarity. In welding, polarity refers to the direction of current flow, which can significantly impact the quality and characteristics of the weld. This article will explore the two main types of welding polarity: reverse polarity (DC+) and straight polarity (DC-), as well as alternating current (AC) welding, highlighting their differences, applications, advantages, and disadvantages.
Understanding Polarity in Welding
Polarity in welding is primarily associated with direct current (DC) welding processes, but alternating current (AC) is also commonly used. Polarity determines the direction in which the electric current flows between the welding electrode and the workpiece. There are three main types of polarity:
1. Reverse Polarity (DC+)
2. Straight Polarity (DC-)
3. Alternating Current (AC)
What Is Polarity In Welding?
Polarity refers to the direction of electrical current flow between the welding electrode and the work clamp, which completes the welding electrical circuit.
Understanding polarity is crucial as it influences electrode consumption and melting rate, heat distribution in the base metal, and the final appearance of the weld bead. Polarity directly impacts the strength and quality of your weld.
Understanding Polarity In AC & DC Welding
There are also two types of current when welding: direct current (DC) and alternating current (AC). Generally, low cost welding machines tend to be DC only, while costlier machines use AC/DC, capable of both.
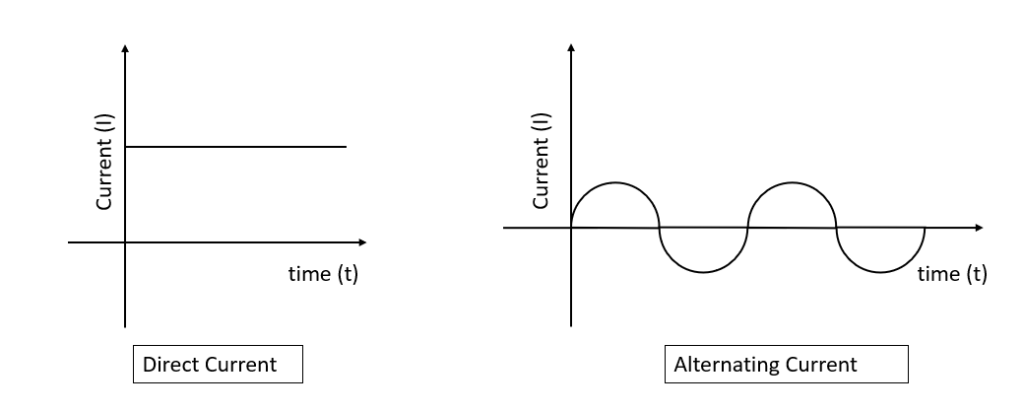
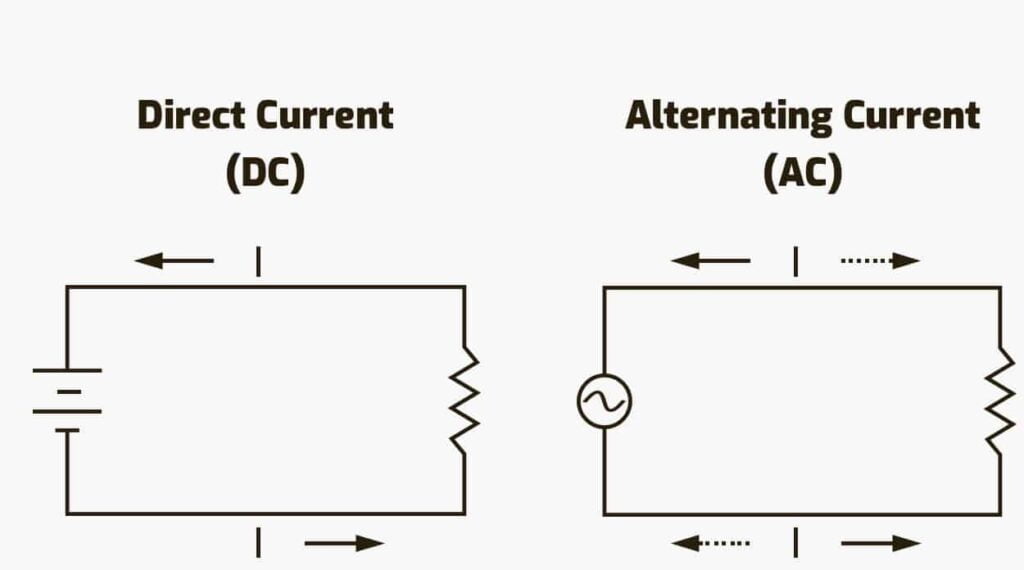
DC and AC current Flow
In short, DC only flows in one direction, keeping it in constant polarity. AC, on the other hand, shifts its flow half the time in one direction and half the other, alternating its polarity from positive to negative 50 times per second in a 50-hertz.
As DC can only flow in one direction, it breaks into two polarity options:
- DC electrode positive (DCEP), also called reversed polarity
- DC electrode negative (DCEN), also called straight polarity.
Most arc welding works best with DC because it provides a more stable arc with less spatter. AC works well with specific applications like aluminum and magnesium when TIG welding.
Straight Polarity – DC Electrode Negative (DCEN)
In straight polarity, also known as DC negative (DC-), the electrode is connected to the negative terminal of the power source, and the workpiece is connected to the positive terminal. This means that the current flows from the electrode to the workpiece.
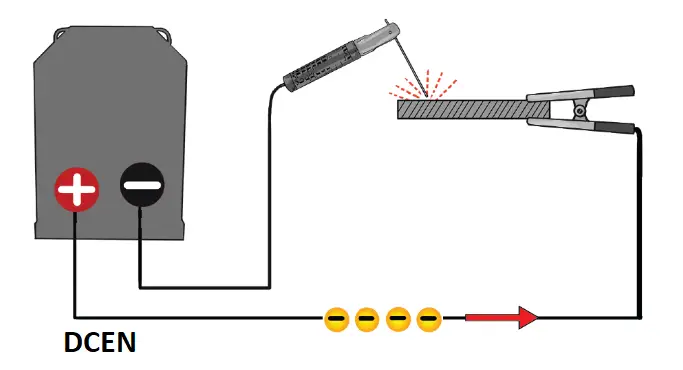
When welding with straight polarity, your electrode will be negative, and your workpiece will be positive.
Because electrons flow from negative to positive, about 70% of the arc heat is concentrated on the electrode, leaving only around 30% at the workpiece.
This results in a wide but shallow weld puddle, a higher burn-off rate of the electrode, and an increased deposition rate.
Straight polarity is advantageous for welding thin materials since the workpiece doesn’t heat up as much. However, the reduced heat in the base metal means there won’t be sufficient electrode oxidation, leading to inadequate impurity removal.
Characteristics and Advantages – DC Electrode Negative (DCEN):
Deeper Penetration: DC+ polarity provides deeper penetration into the base material, making it suitable for welding thicker materials.
Cleaner Welds: It tends to produce cleaner welds with less spatter.
Better for Out-of-Position Welding: Reverse polarity is often preferred for out-of-position welding (e.g., vertical or overhead) because of its stable arc and better control.
Disadvantages – DC Electrode Negative (DCEN):
Higher Heat Input: The high heat input can lead to warping or distortion in thinner materials.
Potential for Excessive Penetration: This can result in burn-through or defects in thin materials.
Applications:– DC Electrode Negative (DCEN):
Used in welding processes like Shielded Metal Arc Welding (SMAW), Gas Tungsten Arc Welding (GTAW), and Flux-Cored Arc Welding (FCAW).
Ideal for welding heavy plates and structural components.
Reverse Polarity – DC Electrode Positive (DCEP)
In straight polarity, also known as DC negative (DC-), the electrode is connected to the negative terminal of the power source, and the workpiece is connected to the positive terminal. This means that the current flows from the electrode to the workpiece.
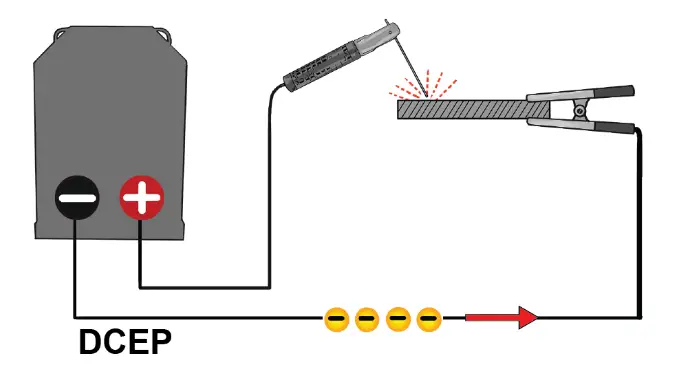
When welding with reverse polarity, your electrode will be positive, and your workpiece will be negative.
In this circuit, we’re stopping the negative half cycle of AC. The electrons will flow from your workpiece to your electrode.
The extra heat on your workpiece will create a narrow weld bead with more penetration and slower electrode consumption, making bead control easier to get a more desirable-looking weld.
This extra heat in the parent metal will now melt it easier and faster, creating a hotter weld puddle, causing electrode oxidation, and removing impurities that will burn off and infuse in the slag.
Characteristics and Advantages – DC Electrode Positive (DCEP):
Shallower Penetration: DC- polarity results in shallower penetration, which is beneficial for welding thin materials.
Higher Deposition Rates: It allows for higher deposition rates, making it efficient for welding processes that require fast build-up of weld metal.
Reduced Heat Input: Less heat is generated in the workpiece, reducing the risk of warping or distortion.
Disadvantages– DC Electrode Positive (DCEP):
Limited Penetration: May not provide sufficient penetration for thicker materials, leading to weaker welds.
More Spatter: Can produce more spatter, requiring additional cleanup.
Applications– DC Electrode Positive (DCEP):
Commonly used in processes like Gas Metal Arc Welding (GMAW) and Submerged Arc Welding (SAW).
Suitable for welding thin sheets and metals that are prone to distortion.
Alternating Current (AC) Welding
Alternating current (AC) welding involves the current switching direction periodically. This means the electrode alternates between being positive and negative.
With AC, you experience alternating straight and reverse polarity half-cycles consecutively. This results in both the benefits and drawbacks of each polarity.
In AC welding, the electron flow changes direction 120 times per second, balancing the heat between the electrode and the workpiece, making it a versatile option.
Advanced welding machines offer settings to adjust the frequency, allowing you to fine-tune arc characteristics, weld puddle behavior, bead profile, penetration, and appearance.
Characteristics and Advantages– Alternating Current (AC) Welding:
Balanced Heating: AC welding provides a balanced amount of heat to both the electrode and the workpiece, which can be beneficial for certain materials.
Ideal for Magnetized Materials: AC is effective for welding magnetized materials where DC would cause arc blow.
Versatility: AC can be used with a wide range of materials and welding positions.
Disadvantages – Alternating Current (AC) Welding:
Less Stable Arc: AC can produce a less stable arc compared to DC, making it harder to control.
Increased Spatter: Tends to generate more spatter than DC welding.
Applications – Alternating Current (AC) Welding:
Commonly used in welding aluminum and magnesium.
Suitable for applications where arc blow is a problem.
How Polarity Affects Welding Performance
Now that you have an overview of the different welding polarities, let’s take a closer look at how each one affects welding performance.
Weld Deposition
DCEP (Reverse Polarity): With 70% of the heat on the positive terminal, DCEP provides high weld deposition, ideal for larger fillet welds and deeper groove welds.
DCEN (Straight Polarity): Offers a lower deposition rate, making it suitable for thinner materials and smaller welds.
Penetration
DCEP: Typically provides deeper penetration into the workpiece, making it suitable for joining thicker materials.
DCEN: Offers shallower penetration, suitable for thin materials or when less penetration is desired, such as in partial joint penetration.
Base Plate Cleaning
DCEP: Provides excellent cleaning action as it heats the parent metal, causing oxides to transfer into the weld puddle and burn off.
DCEN: Does not offer any cleaning action.
AC: Offers some cleaning action, balancing the benefits of both DCEP and DCEN.
Reinforcement
DCEP: Provides great reinforcement due to deeper penetration.
DCEN: Offers poor reinforcement.
AC: Falls somewhere in between, offering moderate reinforcement.
Heat-Affected Zone (HAZ)
DCEN: Creates a wider HAZ since 70% of the heat is in the electrode.
DCEP: Results in a narrower HAZ.
Weld Bead Appearance
DCEP: Easier to control, resulting in a good-looking weld.
DCEN: Harder to control, often leading to a poorer bead appearance.
Electrode Capacity
DCEN: Allows the electrode to burn slower, enabling a significant increase in amperage. This higher amperage leads to a higher deposition rate and shallow penetration.
Heat Balance
DCEN: 70% of the heat is concentrated on the electrode and 30% on the workpiece.
DCEP: The reverse is true, with 70% of the heat on the workpiece and 30% on the electrode.
Understanding heat balance is crucial for mastering welding polarity, as it influences all other aspects of the welding process.
Conclusion
Understanding the differences between reverse polarity (DC+), straight polarity (DC-), and alternating current (AC) is essential for achieving optimal welding results. Each polarity has its unique advantages, disadvantages, and applications, making it crucial to choose the right one based on your specific welding requirements. By mastering the concept of polarity, welders can ensure stronger, cleaner, and more efficient welds, contributing to the overall quality and durability of the welded structures.