Tungsten Inert Gas (TIG) welding, also known as Gas Tungsten Arc Welding (GTAW), is a highly precise and versatile welding process used in various industries. One of the key components in TIG welding is the tungsten electrode. These electrodes come in various types, each designed for specific applications and materials. In this article, we will explore the world of TIG tungsten electrodes, their types, and usage, with the help of a color chart for easy reference.
Selecting the right tungsten electrode is an essential part of TIG welding. The current polarity, power source, thickness of the material, and metal type play a role in tungsten selection. Correctly matching the tungsten electrode with a weld’s requirements saves time and money. But more importantly, it reduces the effort needed to get the clean TIG welds because it drastically improves the welding performance.
The Importance of Tungsten Electrodes
Tungsten electrodes are crucial in TIG welding because they act as the conductor for the electric arc that generates the heat needed to melt the base metal and create a weld. What makes tungsten an excellent choice for this purpose is its high melting point and low rate of consumption. Tungsten can withstand the high temperatures of the TIG welding process, ensuring that the electrode remains stable and doesn’t burn away as quickly as other materials would.
Types of Tungsten Electrodes
Tungsten electrodes come in different types, each suitable for specific welding applications. The choice of electrode type depends on the type of material being welded and the welding conditions.
To simplify things, each of the different tungsten electrodes is designated with a unique code and color.
The oxides are primarily thorium, lanthanum, zirconium, and cerium. Their addition can vary between 0.7 and 4%.
The color chart below summarizes the various TIG tungsten electrodes you may come across:
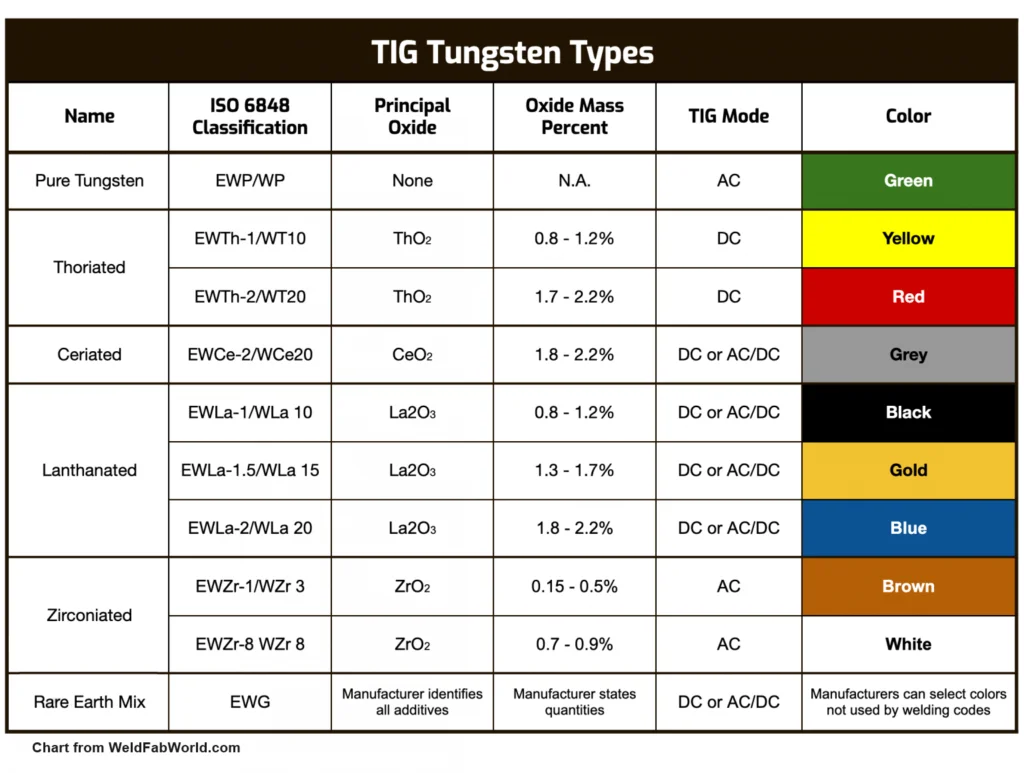
Here are the most common types of tungsten electrodes:
1. Pure Tungsten (Color Code: Green)
Pure tungsten electrodes, identified by their green color code, are primarily used for welding non-ferrous metals such as aluminum and magnesium.
They have a pointed tip and work well with AC (alternating current) welding. However, they are not suitable for welding steel due to the risk of tungsten contamination.
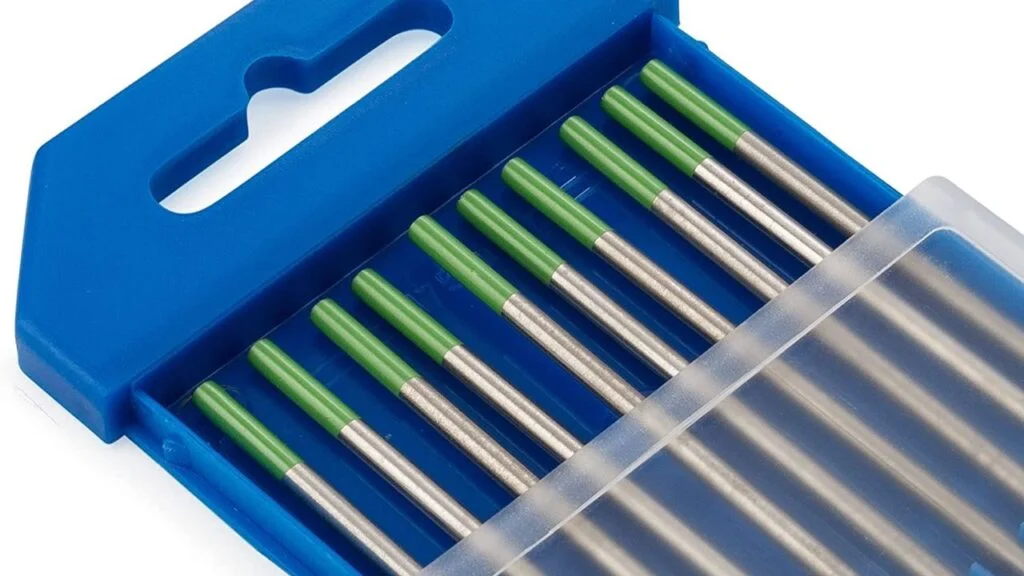
2. Thoriated Tungsten (Color Code: Red)
Thoriated tungsten electrodes are red and are one of the most popular choices for TIG welding. They are excellent for welding steel and stainless steel and are known for their ease of use and long life. However, thorium, a radioactive element, is used in the alloy, so safety precautions must be taken when handling and grinding these electrodes.
Yellow EWTh-1/WT10 : Principal Oxide: 0.8-1.2% Thorium Oxide (ThO₂)
Red EWTh-2/WT20 : Principal Oxide: 1.7–2.2% Thorium Oxide (ThO₂)
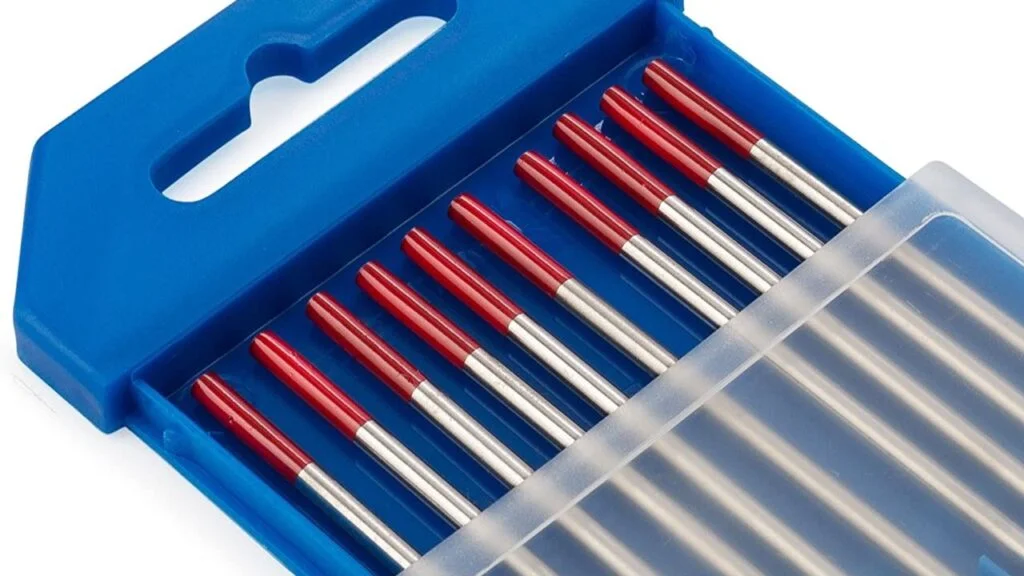
3. Ceriated Tungsten (Color Code: Grey, Formerly Orange)
Ceriated tungsten electrodes, now colored grey but formerly orange, contain about two percent of cerium oxide (ceria). These electrodes have an easier arc start and stability compared to pure tungsten electrodes. Unlike thoriated electrodes, ceriated electrodes are not radioactive and can be used equally well with AC and DC. They are characterized by low erosion rate and a long service life.
Grey Ceriated Tungsten : EWCe-2/WCe20
Principal Oxide: 1.8-2.2% Cerium Oxide (CeO₂)
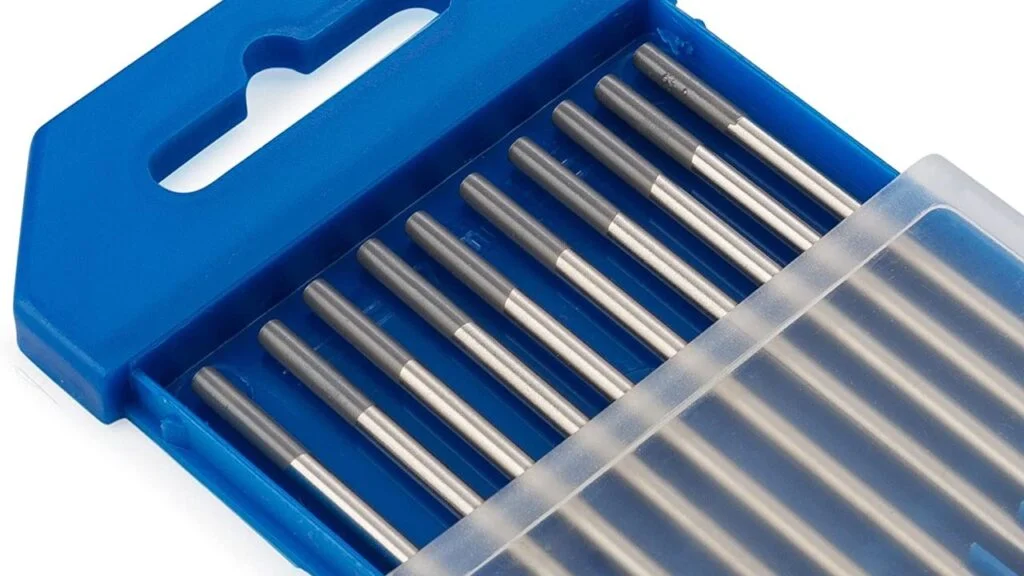
4. Lanthanated Tungsten (Color Codes: Black, Gold, Blue)
Lanthanated tungsten electrodes have similar characteristics as ceriated ones. They contain lanthanum oxide (lanthana) and aren’t radioactive. In general, lanthanated electrodes are characterized by excellent arc starts and stability, low erosion rate, and great re-ignition ability. The black, gold, and blue colors represent different lanthanum oxide percentages, each suitable for specific applications.
Black EWLa-1/WLa 10 : Principal Oxide: 0.8-1.2% Lanthanum Oxide (La2O₃)
Gold EWLa-1.5/WLa 15 : Principal Oxide: 1.3-1.7% Lanthanum Oxide (La2O₃)
Blue EWLa-2/WLa 20 : Principal Oxide: 1.8-2.2% Lanthanum Oxide (La2O₃)
5. Zirconiated Tungsten (Color Codes: Brown, White)
Zirconiated tungsten electrodes contain zirconium oxide (zirconia). They are used when tungsten contamination of the weld pool must be brought to a minimum. The brown and white colors represent different zirconium oxide percentages, each suitable for specific applications.They can’t be used with DC. However, AC current is ideal because zirconia tungsten retains a balled end while minimizing weld contamination.
Brown EWZr-1/WZr 3 : Principal Oxide: 0.15-0.5% Zirconium Oxide (ZrO₂)
White EWZr-8 WZr 8 : Principal Oxide: 0.7-0.9% Zirconium Oxide (ZrO₂)
Using the Color Chart
To select the appropriate tungsten electrode for your TIG welding project, you can refer to the color code. The color-coded bands on the electrodes’ packaging make it easy to identify the type. Remember that the right choice of electrode contributes to the quality and efficiency of your weld.
What Is Purple Tungsten Used For?
The purple tungsten is a rare-earth electrode that replaces thoriated tungsten without residual radioactivity. Its ease of use and narrow arc makes it preferred for GTAW stainless steel.
What Is Orange Tungsten?
The orange tungsten is the old color code for what is now the grey tungsten electrode. The 2% Ceriated Tungsten is best at low amperage ranges and performs well with A/C or D/C applications using inverter or transformer-based constant current power sources. They are great for welding low-alloyed steels, non-corroding steels, aluminum, magnesium, titanium, nickel, and copper.
What Is The Green Tungsten?
The green is a pure tungsten electrode that provides good stability when welding with alternating (“AC”) but may be used with direct current (“DC”) and argon or helium shielding gas. They are typically cheaper, have a lower current-carrying capacity, and lower resistance to weld contamination.
Conclusion
TIG welding is difficult to master, but improper tungsten selection is often the cause of poor-quality welds. If you match TIG electrodes with the applications they are designed for, you’ll significantly improve weld quality. Finding a tailored rare earth tungsten electrode will be your best bet if you need to weld specialty metals in unusual conditions. However, for most welding applications, you’ll do well with either thoriated, lanthanated, or zirconiated electrodes.
Some of these electrodes have overlapping characteristics, but they do have differences. You may need to do some trial and error to find the proper electrode type and size to get the desired results on a specific metal and thickness. Keep testing things. There is no substitute for hands-on experience. The tungsten classification is only one of the many TIG welding variables that determines the best performing tungsten electrode for a given weld.