The updated ASME B31.3-2024 edition brings renewed attention to a critical design parameter in high-temperature piping systems – the Weld Joint Strength Reduction Factor (W). This factor plays a pivotal role in ensuring the integrity, safety, and reliability of piping systems exposed to elevated temperatures.
In this article, we’ll explore what Factor W is, when it’s applied, how it influences design decisions, and what the latest Table 302.3.5-1 tells us about different materials and temperatures.
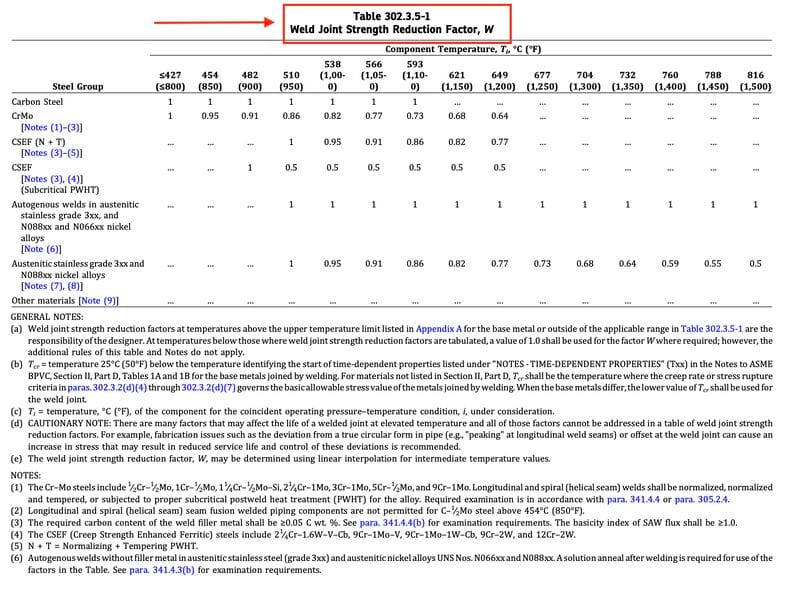
What is Weld Joint Strength Reduction Factor (W) in ASME B31.3?
The Weld Joint Strength Reduction Factor (W) accounts for the reduced strength of welded joints at elevated temperatures. Unlike the base metal, the weld area can undergo changes in metallurgical properties, making it more susceptible to creep deformation and long-term weakening under sustained heat and stress.
ASME B31.3 mandates the use of Factor W for certain materials and temperature ranges where weld strength degradation is significant. Factor W values range from 1.0 (no reduction) to as low as 0.5, depending on temperature and material type.
Source of W Values: Table 302.3.5-1
The 2024 revision of ASME B31.3 includes an updated Table 302.3.5-1, titled “Weld Joint Strength Reduction Factor, W”. It presents W values across several steel groups and temperature ranges—from ambient to 816°C (1500°F).
Example Highlights from the Table:
Carbon Steel retains a factor of 1.0 throughout the temperature range.
CrMo Steels (like 1¼Cr-½Mo) begin to see reductions above 427°C (800°F), dropping to 0.5 at 816°C (1500°F).
CSEF Steels like Grade 91 (P91) see W drop from 1.0 at room temperature to 0.71 at 593°C, and 0.58 at 732°C.
Austenitic Stainless Steels also show decreasing W values beyond 538°C, indicating weakening weld zones at elevated temperatures.
When is Factor W Required in Piping Design?
Factor W is required for materials and temperatures above the upper temperature limit specified for base materials in Appendix A of ASME B31.3. In simple terms, whenever you’re designing for high-temperature services, you should evaluate whether W applies.
Use Weld Joint Strength Reduction Factor (W) when:
Material is susceptible to creep or weld degradation.
The service temperature is above 427°C (800°F) for certain steels.
Weld joints are not heat-treated appropriately (e.g., no PWHT when required).
The code explicitly demands W for that material and joint configuration.
How to Calculate Allowable Stress Using Factor W
Factor W is used to adjust the allowable stress in the weld joint area:
Allowable Stress (Adjusted)=Base Allowable Stress×W
This adjusted stress is then used in wall thickness and pressure calculations to ensure that the design remains within safe limits, considering potential weld weakening.
Example:
If the allowable stress for P91 steel at 649°C is 20 ksi, and W = 0.64,
Then the effective allowable stress at the weld is: 20×0.64=12.8 ksi20 \times 0.64 = 12.8 \, \text{ksi}20×0.64=12.8ksi
Why is Factor W So Important?
Ensures Realistic Strength Assessment
Using Factor W helps avoid overestimating the strength of welds in high-temperature services, where creep and thermal degradation are real risks.
Increases Piping Reliability
Factoring in W leads to conservative, yet realistic, designs that improve the long-term reliability and service life of the piping system.
Prevents Premature Failures
By properly adjusting allowable stresses in welded joints, engineers can prevent unexpected failures due to creep rupture, especially in critical services like power generation, refining, and petrochemicals.
Supports Code Compliance
Applying W aligns your design with the latest ASME B31.3-2024 requirements, helping meet inspection, audit, and regulatory standards.
Important Notes from the Code
- W applies only above the temperature limits specified for the base metal in Appendix A.
- For materials not listed in Table 302.3.5-1, use W = 1.0 unless required otherwise.
- When multiple factors affect joint strength (e.g., weld type, geometry, lack of PWHT), they must be considered collectively in determining W.
- For autogenous welds in stainless steels (without filler), lower W values may be required depending on service conditions.
Applications in Industry
Weld Joint Strength Reduction Factor is critical for:
- Power Plants – Steam lines, HRSG piping, superheaters
- Refineries – High-temp reactors, process piping
- Chemical Plants – Heat exchangers, sulfuric acid lines
- Fertilizer & Petrochemical Units – Ammonia, urea, and reformer tubes
Final Thoughts
The introduction and enforcement of Weld Joint Strength Reduction Factor (W) in ASME B31.3-2024 reflect the industry’s shift toward data-driven, failure-resistant piping design practices. As operating temperatures and service demands increase, the risks to weld joints also grow. Engineers and designers must incorporate W values into every applicable design scenario.
Join us on other platforms
Facebook : https://www.facebook.com/WeldFabWorld/
Instagram : https://www.instagram.com/weldfabworld
YouTube : https://www.youtube.com/@weldfabworld
X Account : https://x.com/Weldfabworld
Telegram : https://t.me/weldfabworld
WhatsApp Channel : https://whatsapp.com/channel/0029Va5YviXCcW4ksGsjNz1G