There are five major types of welding joints. You have to differentiate between a joint and a weld.
This article will teach you how to do that and how to easily recognize each welding joint type as soon as you see it.
Welding joints are used to describe the way two pieces of metal are joined together using welding techniques. There are several types of welding joints, each with its own specific configuration and purpose. Here are some common types of welding joints
Types Of Welding Joints
- Butt Joint
- Lap Joint
- Edge Joint
- Tee Joint
- Corner Joint
AWS says that a joint is simply “The junction of member or the edges of the members that are to be joined”. Therefore the five welding joint types are simply five different ways of fitting two pieces together.
However, each of the welding joint types can be welded in place using many different weld types.
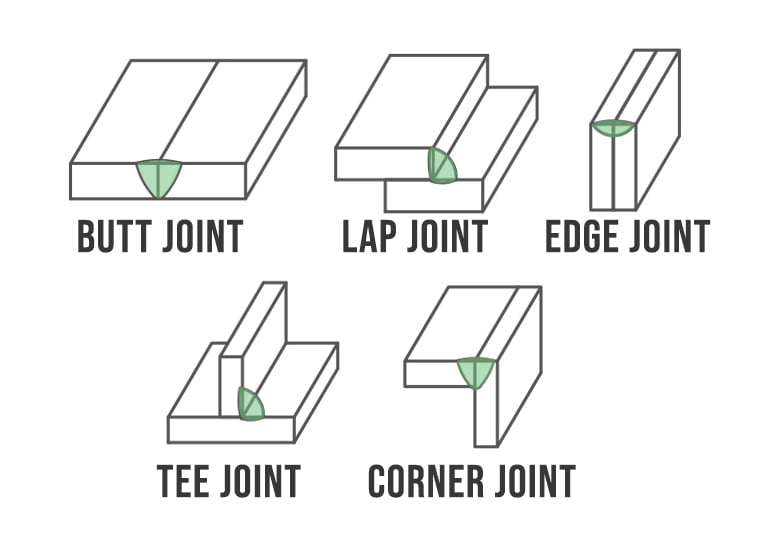
There are many different types of welds and some of them are fillet welds, groove welds, flange, bevel, surfacing, backing, plug, slot and etc.
Basically, there are 5 major joint types and each can be welded with many different types of welds.
Butt Joint Welding
A butt joint in welding is a type of joint configuration where two pieces of metal are aligned in a nearly end-to-end manner and joined together at their adjacent edges. This type of joint is one of the most common in welding applications, especially when joining two pieces of metal with thicknesses that are nearly the same. Butt joints are used in various industries, including construction, manufacturing, and metal fabrication.
The area between the pieces is prepared if necessary and welded. In the preparation phase, we will choose the weld type.
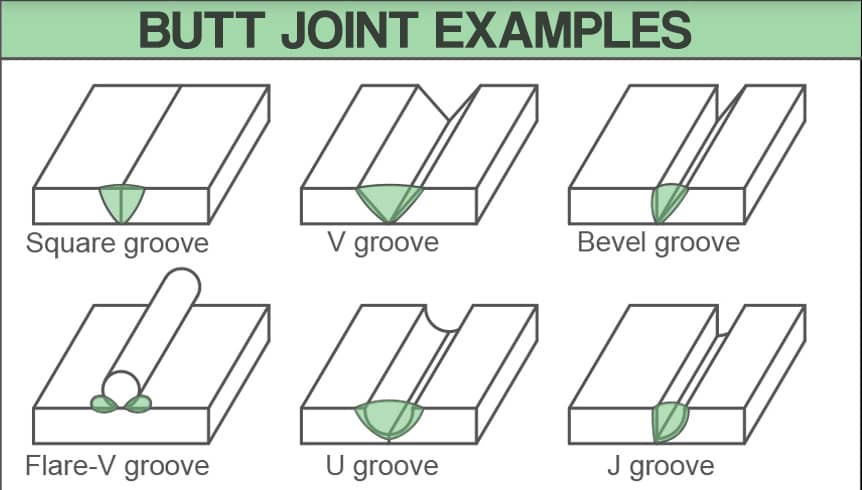
It will be either a simple square groove with or without a root opening between the pieces or you may shape the edges so that you get a V groove, J grove or similar (shown on image).
The most typical butt joint types of welds are:
- Square Groove
- V Groove
- Bevel (Single and double)
- Flare V Groove
- U Groove (Single and double)
- J groove ((Single and double)
Butt joints are essential in welding because they provide a direct and efficient way to connect two pieces of metal along their edges. Proper preparation and welding techniques are critical to create welds that meet the necessary structural and quality requirements for the intended application.
Lap Joint Welding
A lap joint in welding is a type of joint configuration where two pieces of metal overlap each other partially or entirely and are joined together at the overlapping portion. It is one of the most common joint types used in various welding applications, particularly when joining two pieces of metal of similar thickness. Lap joints are widely used in manufacturing, construction, and metal fabrication.
The lap joint is usually used to weld together two base metal pieces to each other of different cross-section thicknesses. This makes it difficult to achieve a proper butt joint which is why the lap joint makes a better choice.
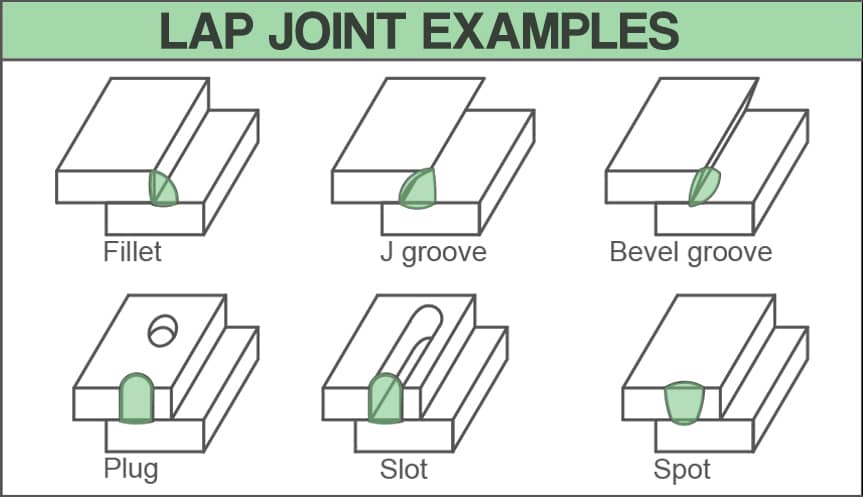
There are other reasons why a lap joint may be preferred but this is the most common one. You can apply various types of welds to lap joint and commonly used are:
- Fillet weld
- J groove weld
- Bevel groove weld
- Plug welds
- Slot welds
- Spot weld
Lap joints are versatile and widely used because they provide a simple and effective way to connect two pieces of metal. However, the choice of welding process, joint design, and welding technique should be carefully considered to ensure the resulting weld meets the specific requirements of the application.
Tee Joint Type
A tee joint in welding is a type of joint configuration where two pieces of metal are joined together to form a “T” shape. It is a common welding joint used in various industries, including construction, manufacturing, and metal fabrication. The tee joint is used when one piece of metal needs to be attached perpendicular (at a right angle) to another piece of metal. This configuration allows for the creation of structures, frames, and components with different shapes and sizes.
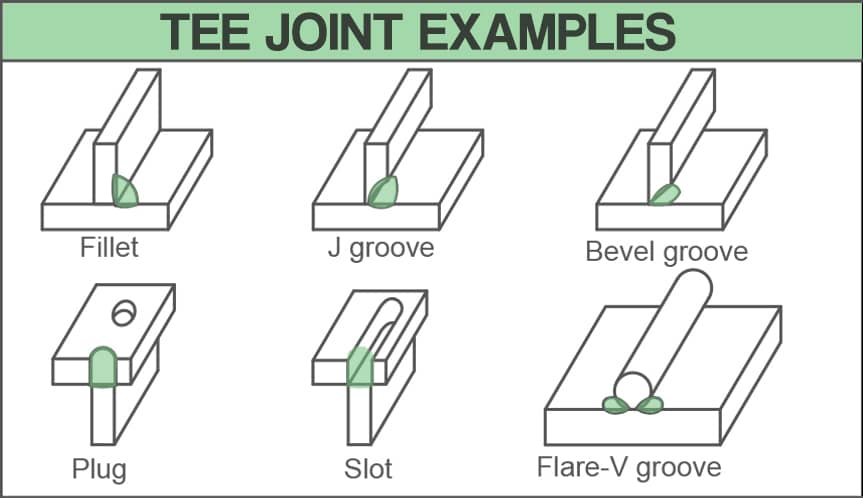
Tee joints are used in a wide range of applications, from constructing steel frames in buildings to fabricating automotive components and manufacturing machinery. Welders must have the skills and knowledge to prepare and weld tee joints effectively, as the quality of the weld can significantly impact the strength and performance of the final product.
T weld joints can be achieved with multiple welding styles and these are the commonly used:
- Fillet
- J groove type weld
- Bevel groove weld
- Plug weld
- Slot weld
- Flare V groove weld
The welding joints are not commonly prepared with groove before they are welded to each other. If the welding project consists of very thick base metal then joint preparation will definitely be necessary. Common welding practices require that the filler metal makes a strong connection with the base plate on both sides of the weld.
Corner Joint Welding
A corner joint in welding is a type of joint configuration where two pieces of metal meet at a right angle, forming a corner. This type of joint is common in various welding applications and is used when the pieces need to be joined perpendicularly. Corner joints can be found in many industries, including construction, fabrication, and manufacturing.
The corner weld joints can be either in the open or closed state.
These weld joints are very common in sheet metal work and they are achieved with various welding processes.
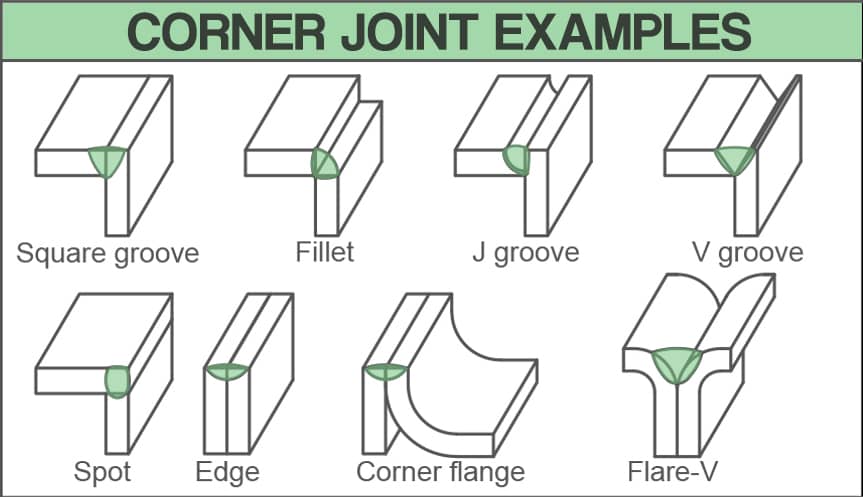
Commonly used weld types are for corner joints are
- Square groove
- Fillet weld
- J groove weld
- V groove weld
- Flare V groove weld
- Spot weld
- Edge weld
- Corner flanging edges
Corner joints are fundamental in welding, as they enable the creation of structures and components with right angles and perpendicular connections. Proper preparation and welding techniques are critical to achieving strong and reliable corner welds that meet the necessary structural and quality requirements for the intended application.
Edge welding joints
Edge welding joints are a type of joint configuration in welding where two pieces of metal are joined along their edges, creating a seam or weld along the edge of the materials. Edge joints are commonly used in various welding applications, particularly when two flat pieces of metal need to be joined end-to-end or side-by-side. These joints are found in industries such as construction, manufacturing, automotive, and metal fabrication.
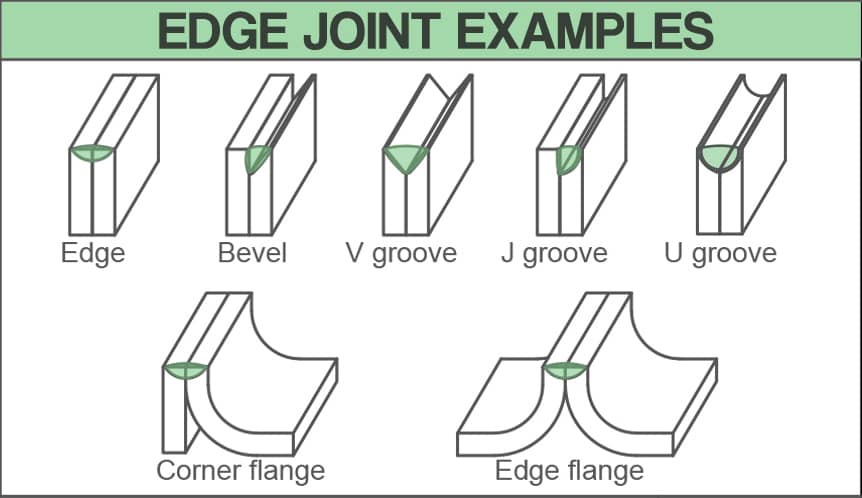
The biggest challenge is when welding thin sheets parts together and when the edge weld configuration is complex.
These welding joints are quite often used with flanged edges sheet metal parts or are used when a weld needs to be made that attaches adjacent edge joints sheet metal elements.
The common weld types:
- Edge welding joint
- Bevel groove weld
- V groove welds
- J groove weld
- U groove weld
- Corner flange
- Edge flange, flanging edges
These are versatile and are used extensively in welding applications because they allow for the creation of seams and connections along the edges of metal materials. Proper preparation and welding techniques are crucial to achieving strong and reliable edge welds that meet the necessary structural and quality requirements for the intended application.
Want to learn about welding symbols associated with weld types and welding visit our article : Welding Symbols