Welding porosity refers to the presence of small cavities or voids in a welded joint. These voids can weaken the weld and compromise its integrity. Porosity in welding is undesirable because it can lead to structural problems, reduced strength, and even weld failure. Understanding the causes, prevention, and fixes for welding porosity is essential for producing high-quality welds.
Porosity is defined as “Cavity-type discontinuities formed by gas entrapment during solidification or in a
thermal spray deposit.” The porosity may be surface or subsurface, a single cavity, aligned, or clustered, and is represented by the following figures.
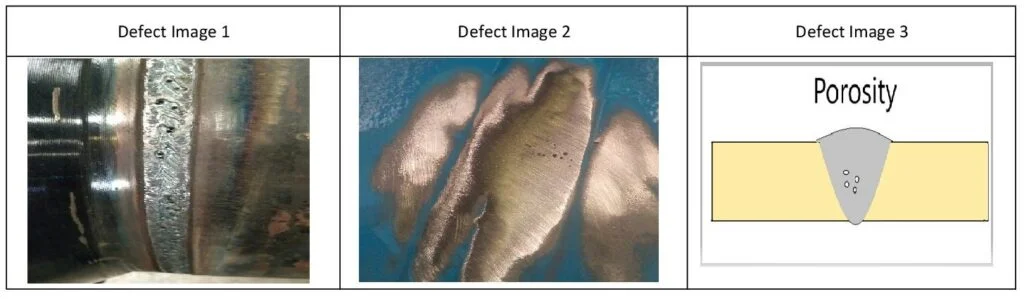
Nothing annoys a welder more than seeing those sparks and small explosions mid-bead, knowing when the hood is lifted, it’s not going to be pretty.
Every welder has experienced weld porosity.
In this article, we will discuss what it is, what causes it, and what we can do about it. for other welding defects please visit
Different Types Of Porosity
There are four types of weld porosity that can manifest in different forms.
Surface Porosity
One of the most obvious forms is surface porosity, also known as surface breaking pores. This is the porosity that looks like swiss cheese to the naked eye.
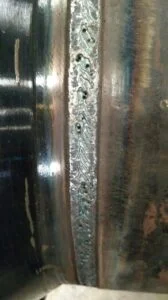
The pores are sitting right on top of the bead, spread out evenly or deposited randomly throughout the bead.
Surface porosity, also known as surface defects or surface discontinuities, refers to irregularities or imperfections found on the external surface of a material, typically a metal or a weldment.
Surface porosity is a common concern in welding and manufacturing, but with proper techniques, controls, and inspections, it can be minimized or eliminated to ensure the quality and reliability of the final product.
Subsurface Porosity
Subsurface or distributed porosity can also be hidden beneath the surface of the bead. This porosity is harder to detect.
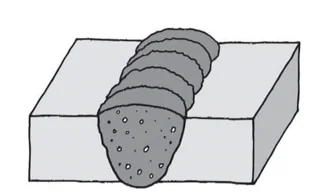
Radiography test or ultrasonic test or a grinder are good tools to discover this form of porosity. This type of porosity can also display itself with a small bubble that expands as the bead cools.
Causes of Welding Porosity:
Below are main causes of porosity which we tried to explain their may be other reasons too
Contaminants in the Weld Pool:
One of the primary causes of porosity is the presence of contaminants such as moisture, oil, grease, rust, or paint on the base metal or filler material. When these contaminants are exposed to the high temperatures of welding, they can release gases that create voids.
Improper Shielding Gas:
In processes like MIG (Metal Inert Gas) or TIG (Tungsten Inert Gas) welding, a shielding gas is used to protect the molten weld pool from atmospheric contamination. If the gas flow rate is incorrect or the gas mixture is improper, it can lead to porosity.
Inadequate Gas Coverage:
If the shielding gas does not completely cover the weld pool or if there are gaps in the gas coverage, atmospheric gases like oxygen and nitrogen can react with the molten metal, causing porosity.
Moisture in Electrodes or Flux:
In stick welding (SMAW) or flux-cored arc welding (FCAW), moisture can be absorbed by the electrode or flux. When the electrode is heated, this moisture can turn into gas and create porosity.
Incorrect Welding Parameters:
Using incorrect welding settings such as too high or too low welding current, improper travel speed, or incorrect electrode angle can result in porosity.
Prevention of Welding Porosity:
To prevent weld porosity below shall be taken care during and before welding
Cleanliness:
Ensure that the base metal and filler material are clean and free from contaminants. Remove rust, paint, oil, and grease before welding.
Proper Shielding Gas:
Use the correct shielding gas and ensure the gas flow rate and mixture are appropriate for the welding process and materials being used.
Gas Coverage:
Ensure that the shielding gas completely covers the weld area without any gaps. Adjust gas nozzles and flow rates as needed.
Dry Electrodes and Flux:
Store electrodes and flux in dry conditions to prevent moisture absorption. Follow manufacturer recommendations for storage or established procedure.
Welding Parameters:
Set the welding parameters according to the specific welding process, material thickness, and joint configuration. Weld within the recommended ranges.
Fixes for Welding Porosity:
- Re-weld: In some cases, porosity can be repaired by grinding out the affected area and re-welding it.
- Change Electrodes: If porosity is due to moisture in the electrodes, replace them with dry electrodes.
- Gas Adjustments: Adjust the shielding gas flow rate and composition as needed to improve gas coverage.
- Clean and Preheat: Clean the base metal thoroughly and preheat it if necessary to remove contaminants and moisture.
- Check Welding Parameters: Ensure that welding parameters are set correctly for the specific welding task.
Preventing welding porosity through proper preparation, equipment, and technique is key to producing strong, reliable welds. If porosity does occur, identifying its root cause and applying the appropriate fix is essential to maintain weld quality.